Gábor Hangosi, from Purman, talks about transforming industrial buildings into designer furniture.
Have you ever wondered what happens to buildings when they reach the end of their useful life? In the past, structures made from natural materials like wood, brick, and stone could easily be repurposed or recycled. But modern buildings, especially those constructed with sandwich panels filled with synthetic materials like polyurethane (PU) foam, present a significant challenge. Unlike timber or stone, PU foam is non-biodegradable and doesn’t break down naturally over time, raising important questions about disposal and repurposing.
PU foam is widely used across various industries due to its excellent insulation properties, lightweight nature, and durability. It’s found everywhere—from buildings and furniture to household appliances like refrigerators. Sandwich panel manufacturers are particularly aware of this issue, as they generate significant waste at multiple stages, making sandwich panel production one of the largest sources of PU foam waste.
During manufacturing, mistakes, production errors, and setup mishaps result in substantial waste. Even when panels are successfully produced, their fixed dimensions often lead to on-site waste during installation. Constructing walls with these panels inevitably results in leftover pieces from trimming or cutting openings for doors and windows. In large industrial buildings, this waste can accumulate to hundreds of square meters. Globally, estimates suggest that PU foam waste from sandwich panel manufacturers ranges between 40,000 and 50,000 tons annually—and that’s just one industry.
Traditionally, PU foam waste ends up in landfills or is incinerated, but both methods have significant downsides. Landfilling PU foam doesn’t solve the problem; it merely postpones it, as the foam doesn’t decompose, leading to long-term space occupation and environmental pollution. As urban areas expand and environmental regulations tighten, finding new landfill sites becomes increasingly difficult.
Incineration, while reducing waste volume, releases toxic chemicals like dioxins and furans into the atmosphere, posing significant health risks including cancer and respiratory issues. Burning PU foam also contributes to greenhouse gas emissions. As global PU foam production continues to rise, these disposal issues will worsen. Without innovative and sustainable solutions, the environmental impact will intensify, threatening ecological balance and public health.
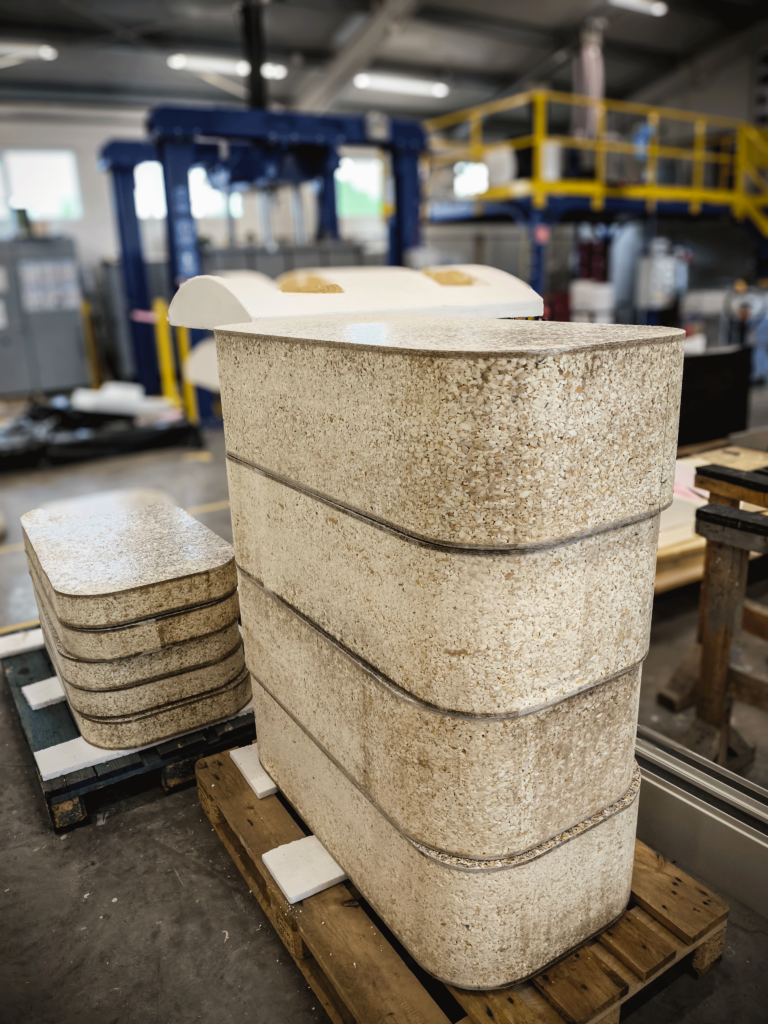
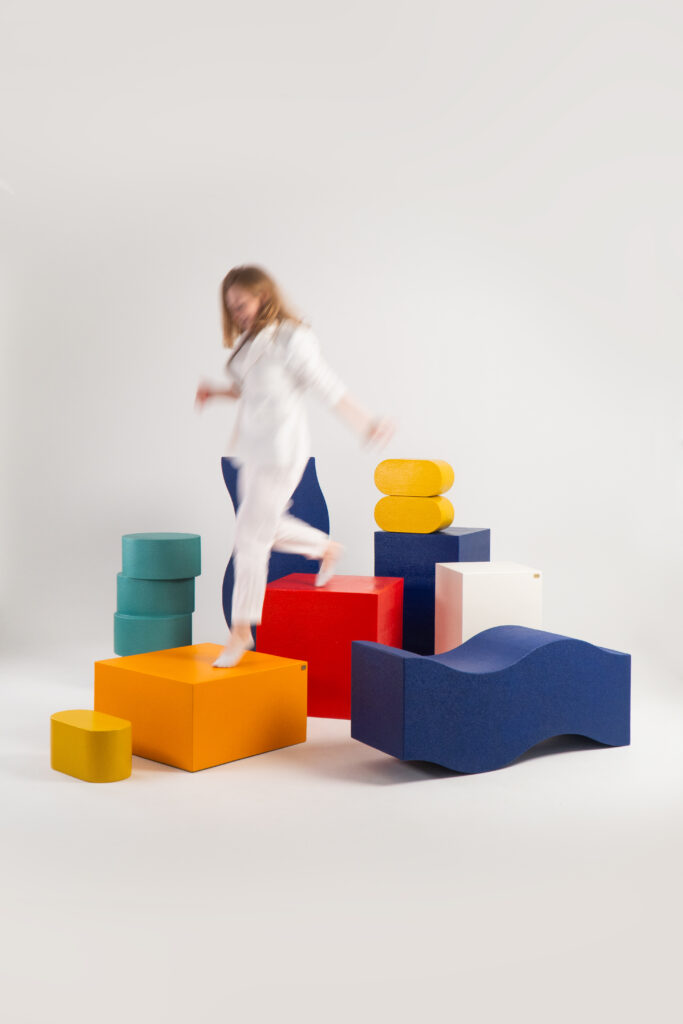
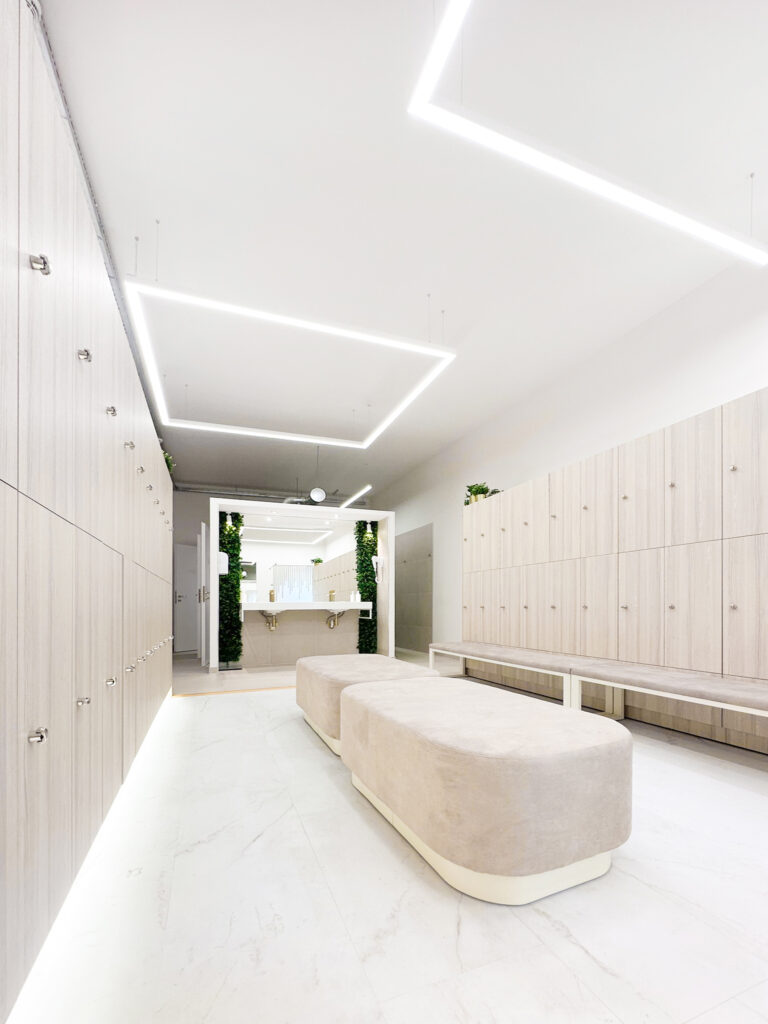
Enter Purman®, a startup that has developed an innovative solution to tackle these environmental challenges. They upcycle PU foam using lignin, a byproduct of the paper industry, to bind the particles together. This method not only repurposes PU foam but also utilizes a natural waste product, creating a more sustainable and circular solution. Imagine turning industrial insulation materials into designer seating furniture and other valuable products—transforming waste into something beautiful and useful.
Why is this method particularly exciting for the furniture industry? The recycled PU foam exhibits exceptional strength and durability, making it ideal for furniture bases and structural components. The integration of lignin enhances the mechanical properties of the material, resulting in furniture pieces that can withstand daily wear and tear, ensuring longevity and customer satisfaction. Robust sofa frames, sturdy table bases, and resilient chair structures can be crafted from recycled materials without compromising on quality.
Safety is also paramount. The natural properties of lignin contribute to improved fire resistance, enabling the recycled PU foam to meet stringent fire safety standards. Furniture made from this material is inherently safer, reducing the risk of fire-related incidents. This makes it perfect for public areas where compliance with fire regulations is mandatory, providing peace of mind for both manufacturers and consumers.
In an era where environmental consciousness influences consumer choices, using recycled PU foam offers a significant advantage. The method is eco-friendly and sustainable, reducing environmental impact by diverting PU foam waste from landfills and incineration. By utilizing lignin—a renewable, plant-based binder—the process minimizes reliance on synthetic chemicals and lowers carbon emissions. Furniture produced this way appeals to environmentally conscious consumers who prioritize sustainability, enhancing brand reputation and marketability.
One of the most exciting aspects for designers is the material’s versatility in design. The recycled PU foam can be molded into various shapes and sizes, allowing for innovative and customizable furniture creations. This flexibility enables designers to push the boundaries of traditional furniture aesthetics, experimenting with unique forms and intricate details. From sleek minimalist chairs to complex geometric tables, the possibilities are vast. Customization also allows manufacturers to cater to specific client needs, offering personalized solutions that stand out in a competitive market.
By integrating these advantages, the furniture industry can contribute to environmental sustainability while benefiting from high-quality, durable, and versatile materials that meet modern consumer demands.
Traditional recycling methods for PU foam often involve high temperatures and complex chemical reactions, consuming significant energy and contributing to greenhouse gas emissions. In contrast, using lignin as a natural binder allows the recycling process to operate at lower temperatures, reducing energy consumption and operational costs. Adopting such economically viable and environmentally sustainable methods is both timely and necessary.
This innovative approach opens up new markets and economic opportunities in the furniture industry. Manufacturers can tap into the growing demand for sustainable products, differentiating themselves in a crowded marketplace. The versatility of products made from recycled PU foam maximizes the value of the recycled material, embodying the very essence of a circular economy.
By transforming waste into high-quality furniture products and utilizing renewable resources, this method helps close the loop, keeping materials in use for as long as possible. It reduces the need for virgin materials, conserves natural resources, and minimizes environmental impact. As the world moves towards more sustainable practices, innovative solutions like this are essential for achieving long-term environmental and economic goals.
Imagine a future where the chairs in our offices, the sofas in our homes, and the seating in public spaces are all made from materials that were once considered waste. With the Purman® method, this future is within reach. Isn’t it time we embraced the possibilities?