British bed manufacturer Hypnos opens up the factory doors as Big Furniture Group explores just how the Royal Warrant holder produces its mattresses.
When venturing outside Norfolk’s predominately flat terrain, most places come with picturesque views. Arriving at the Princes Risborough-based headquarters of bed and mattress maker Hypnos, such views did not disappoint. The absence of rain also helped too!
From the off, the Hypnos showroom was thoughtfully laid out with a nice touch on their rich 120-year history, displayed as soon as you set foot through the door (alongside all of their award wins too). There was even a ‘living wall’ – further endorsing their green credentials.
After a catch up with CEO James Keen over a coffee, this editor was fuelled and raring to explore the facility, a location where Hypnos has been for over 15 years – and one that was formerly a print house.
Leading the tour, a trio of Hypnos’ finest included David Baldry, Group Managing Director, Amanda Castle, Head of Retail Marketing, and Ashley Garside, Head of Operations. It must be said that Ashley’s enthusiasm, commitment and drive to keep improving the factory is second to none and he provided one of the most enjoyable and informative visits yet.
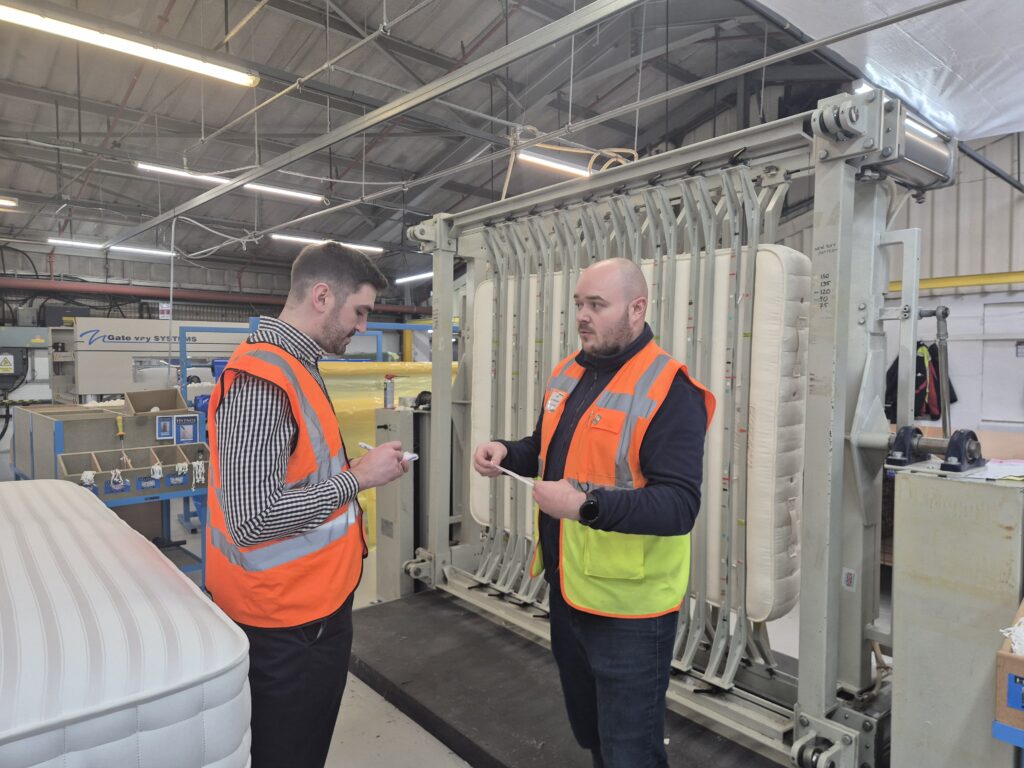
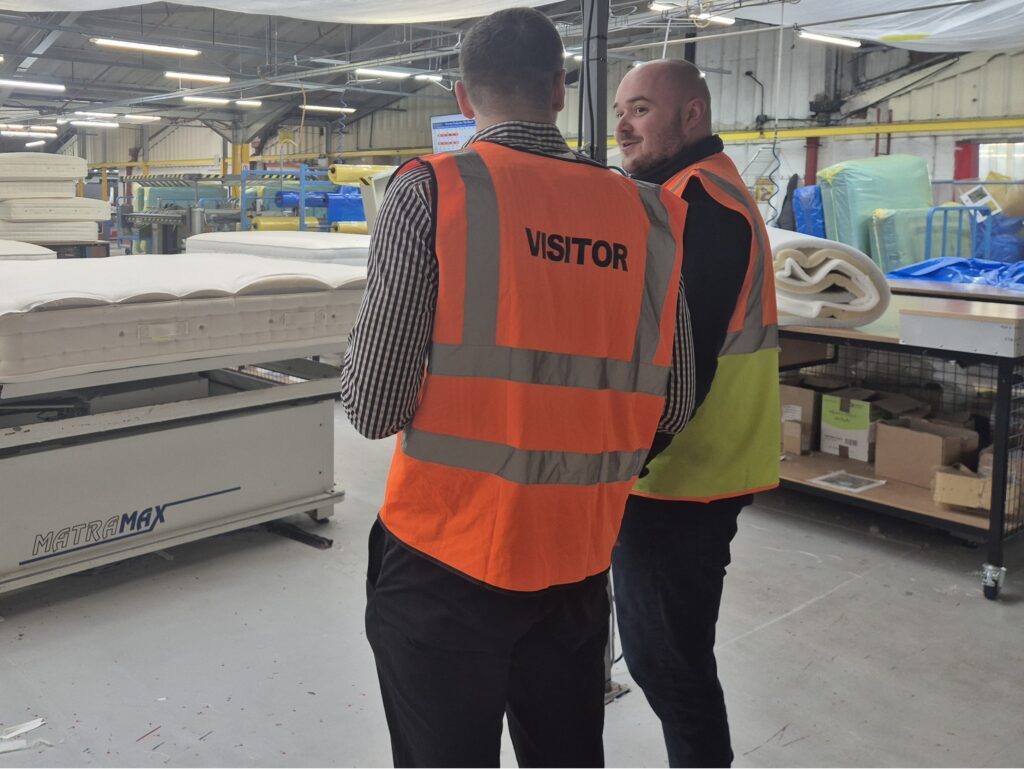
Beginning at the start and also the end, the yard captures the entire process from goods in to goods out in one big circle where they get five to eight deliveries per day, which are unloaded in the ‘Shed’ area and divided into correct storage sections. Also, in the yard was one of Hypnos’ latest investments, its new electric truck – and yes, the opportunity to climb aboard was certainly taken!
Hypnos recently appointed a new transport and logistics partner, DFDS, so customers can continue to benefit from a dedicated fleet with the additions of trackable, sustainable, state-of-the-art delivery systems. The partnership includes a new latest generation Volvo EV and charging points on site, an investment of £750,000. The truck, as displayed at the September Bed Show, is impressive to say the least. It even features cameras to replace traditional wing mirrors that help save 8% on fuel consumption. Hypnos plans to incorporate more Volvo EV trucks to its fleet, with another to join in April 2025, while aiming to reach five to seven by the year end.
It’s fair to say David absolutely loved showing off the truck and all its gadgets. It’s even kitted out with a Hypnos Comfort Mattress in the cabin. It was also while inside the truck, David said: “Key partnerships help the business go further and much quicker.” It was a sentiment that would echo the tour as forging reliable partnerships has allowed the business to do what it does best, make beds.
Furthermore, David revealed that all other trucks within its fleet have changed to sustainable fuel types including renewable bio diesel (HVO) following a successful trial. In keeping on the topic of investments, back in July 2024, Hypnos went live on a new ERP system as part of a £1.5m infrastructure investment, that amongst many benefits enables even deeper traceability for its Red Tractor and RWS wool projects, where 100% British wool is traceable right back to assured farms. David fondly refers to visiting Mary, one of the 21 British RWS certified farms Hypnos supports via Woolkeepers. It’s been an ongoing commitment for the business since 2019 that’s clearly here to stay.
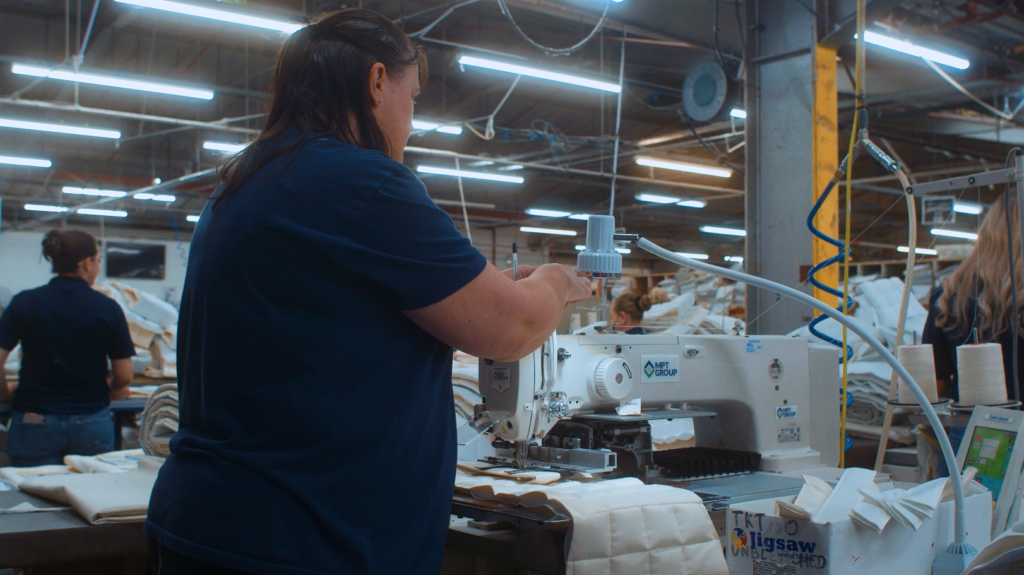
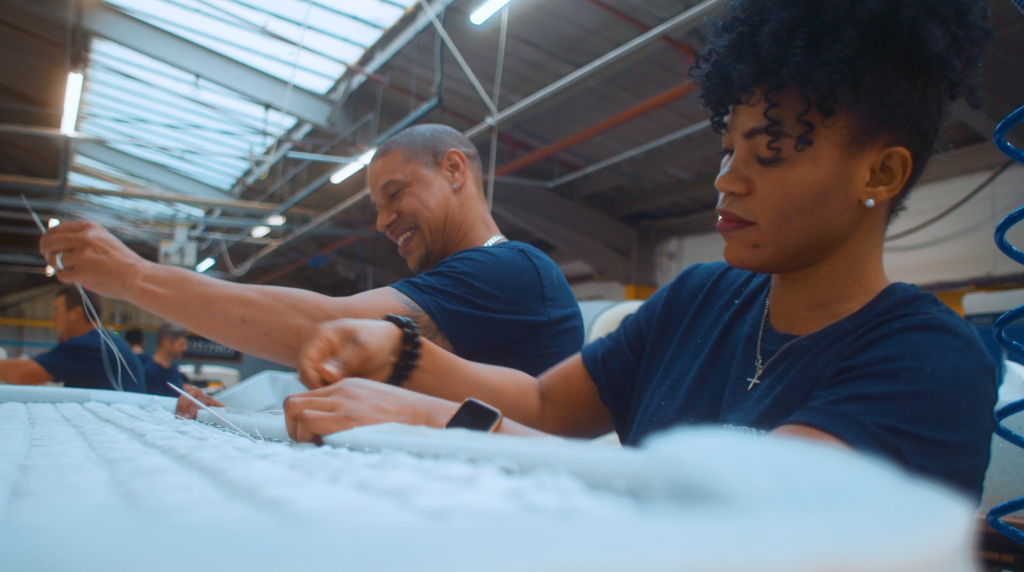
At this point of the tour, we found ourselves in the ‘picking zone’ where the start of a mattress build really takes place. Components are picked and arranged in exactly the right order and layered as such to maximise efficiency as the product moves through the factory. Hypnos only makes products to order too and prides itself on its talented staff, who are all multi-skilled and trained inhouse. In fact, some staff are multi-generations with some workers racking up service spanning over 40 years. There are 160 hands on staff across the factory, while Hypnos currently employs 289 people in total. When walking through each stage, from the offices, logistics, warehousing and of course the factory floor itself, staff were all happy, excited and proud to show off their skillsets. It really has that ‘good feeling’ about the place.
Moving through various areas, watching the staff busy on the production line – Hypnos makes around 390 to 460 units per day, Ashley regularly enforced that attention to detail is everything with staff well drilled at constantly checking at each stage of production. The culture of pride is strong, with any faults not deemed as being negative, but more praised to make sure each product that leaves is of the highest standard. We made a stop at the side stitching area where, using a giant needle, we watched the professionals at work. It can take around 45 to 90 mins to side stitch a mattress, depending on what model, and it takes trainees around eight weeks to learn the job.
Ashley then introduced us to Danny on taping. Now this is something to see. Arguably the highest and hardest skill to master in the factory – it actually takes 20 weeks to learn and some even don’t carry on with it – taping requires fast fingers, a strong knee and super eyesight to whizz around the edges of a mattress. Watching Danny, who has been with the company almost five years, it was like second nature to him. Controlled with the knee to allow for hands to seamlessly stitch through, it looks like a very tricky task and extremely difficult to do at speed. Hat’s off to him!
Moving on brought us to the tuft machine, which presses a mattress ready for tufting. Using another giant needle, stabbing through the layers of a mattress is tough work, where of course the Hypnos staff made it look easy. Tufting ranges from five rows to seven or nine depending on the model. That’s a lot of manual punching!
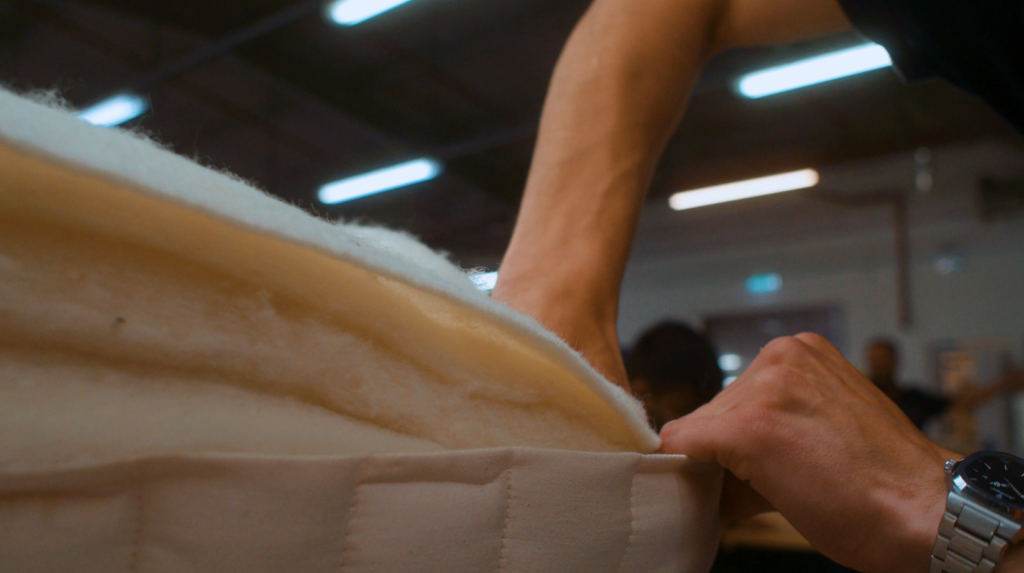
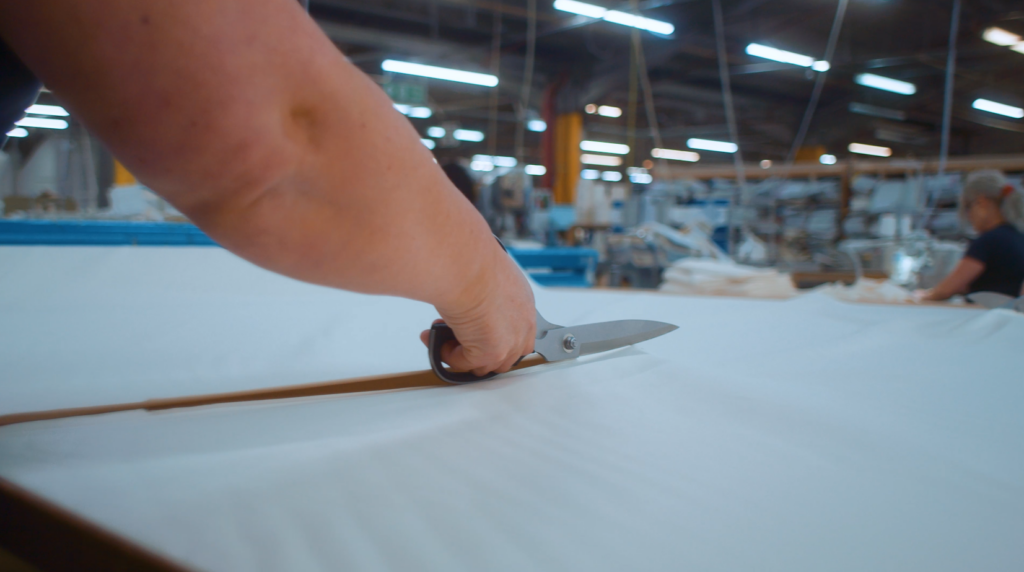
As we continued through, Ashley explained that there are two bags for packaging for added product protection and delivery cleanliness, while the framing section, which leads onto the upholstery and drawer carcasses, is also where testing for drawers takes place. This can take between 20 to 30 minutes to conduct a complete check, while around 260 divans are also produced in this zone. Back to investments, Hypnos has installed a new slitting machine for ticks on mattresses. We met John, who slits them all! Implemented back in July 2024, this has saved “enormous amounts of time and wastage”, says Ashley and is a far cry from the traditional slit machine that relied on hand operation and often tore tick ends.
Ashley added that there is a consistent drive on investing in multi-skilling staff, while future investments in the pipeline include replacing some of the tape edge machines to newer models as well as other improvements across the factory. “Ideas come from the shop floor to help boost efficiency and we keep tools up to date and improve practices further,” Ashley added.
Over the past year, the facility has been creative to incorporate its contract side and other parts of the business that moved across following the end of its lease at Castle Donnington. The final part of the move completed back in September and the focus to streamline all operations from one self-owned facility the “one home of Hypnos” has been remarkable. An achievement David and all of the team at Hypnos are proud of, yet not standing still as Ash is always looking to identify the next improvement.
In fact, on the contract side, Ashley has been busy implementing an infrastructure away from the main factory lines to keep capacity where it needs to be and support the sometimes large demands of this side of the business. On average, this facility alone can produce 325 pieces a day at full operation on a single shift. Other investments throughout include special brighter lighting across the factory floor to help with quality especially on fabrics, the constant focus on detail and quality has reached the floor itself with a refresh in paint to demark flow and areas.
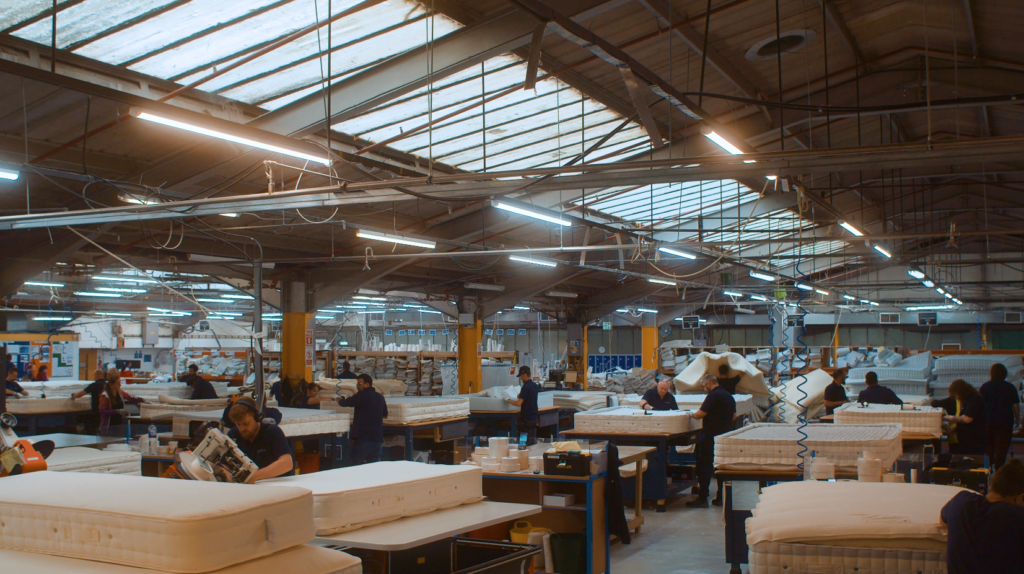
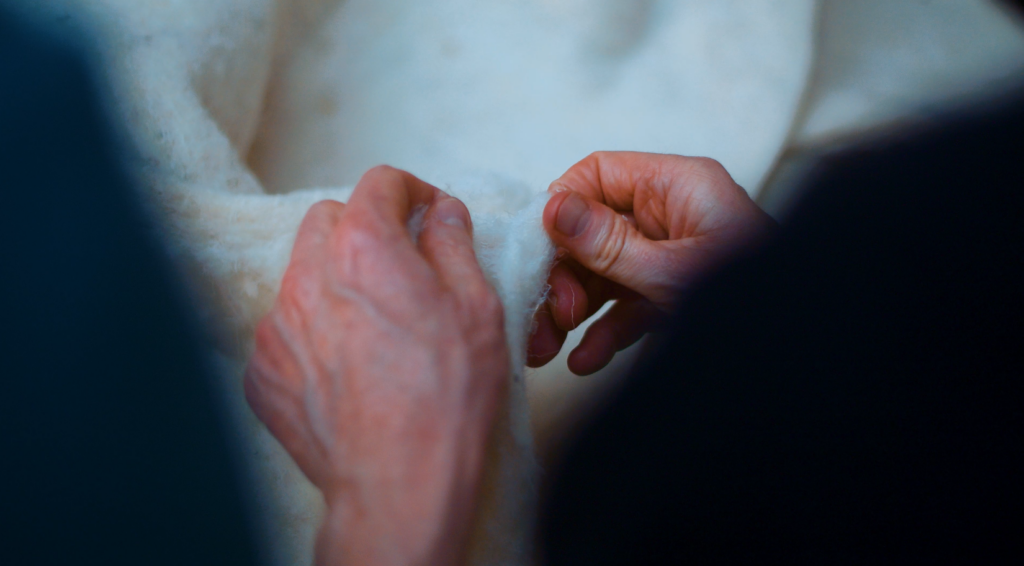
Mark Cort has been appointed as Commercial Director for Hypnos, completing the senior leadership team as the bedmaker looks ahead to continued sustainable growth. Mark will use his experience in the industry to build on its legacy and continue growth in sales of Hypnos beds and mattresses within the retail and hospitality sectors. As with all new employees, staff are encouraged to complete a factory introduction where they can experience elements of the factory and get fully invested in the company and production values – a nice touch that helps build comradery across all aspects of the business.
With 2024 being its 120th legacy year, and 95th as a Royal Warrant Holder, Hypnos moves in 2025 full of optimism at building further growth through establishing partnerships and relying on its bed-making principles. Following a successful Bed Show in September, which included the launches of two new adjustable mattresses, its range of pillow tops, now in two tensions, and fabric collaborations with leading British design houses, as well as a new approach to its Project Zero and the launch of ‘My First Hypnos’ – a partnership with children’s poverty charity Barnardo’s, the business has a solid platform to continue to grow.
Although remaining tight-lipped for now on future partnerships, David echoed the earlier sentiment that “key partnerships are the way forward to grow the business further, and faster”. With the continued investment and infrastructure behind the company firmly in place, the future for Hypnos looks extremely encouraging.
For now, Hypnos can reflect on what has been a massive milestone year for the business and has welcomed this editor back for some hands-on training. So, watch this space, the next Hypnos mattress you see may well have been made (in part) by BFG.
Milestone moments
1904 – Hypnos established
1929 – First Royal Warrant from King George V
1965 – Peter Keen, fourth generation, joins family business
1997 – James Keen, fifth generation, joins family business
2009 – Hypnos moves to current home of Hypnos in Princes Risborough
2011 – Hypnos first Bed manufacturer to become Carbon Neutral
2017 – Queens Award for Enterprise in International Trade
2019 – Hypnos partners the Eden Project and introduces traceable wool via Woolkeepers and Red Tractor assured farms
2020 – Queens Award for Enterprise in Sustainable Development
2022 – Designs first Organic collection – approved by the Soil Association
2023 – Launches first Eden Project Collection with new and unique plant fibres and introduces a global standard for British wool with the Responsible Wool Standard
2024 – 120th year, introduces transport with integrity, with 2 electric vehicles and transfers from diesel to HVO. Launched partnership with Barnardos childrens charity. Invests in British design partnerships. Peter Keens 80th year.
2025 – British Collective, more investment in British farms and wool, continued development of 2030 transport strategy, working with our retail partners.