Following a recent interview with Jag Sandhu, Director at Tokyo Fabrics, on why Halogen FR treatments are important for full compliance, we jumped at the chance to explore the factory to find out more about the company, its ethos and bold expansion plans.
A few months ago, furnishing fabrics supplier Tokyo Fabrics shared a detailed insight about the importance of its continued use of Halogen FR treatments and why quality and safety should never be compromised. In a passionate article, Jag said that he and the company “will not gamble on safety” with a halogen-based application the “clear leader when it comes to FR performance”, as opposed to halogen-free.
So much so, the business has absorbed the higher costs associated with Halogen FR, as if Tokyo Fabrics were to switch to a halogen-free FR formula, the company would make a saving of £60,000 per week – an annual saving of £3million.
“For us, whilst our profits may be getting impacted, our quality is not compromised,” Jag said. “Despite shouldering significant rising costs of Halogen FR, we believe it’s a sacrifice necessary for the peace of mind that underpins our robust track record. Our loyalty to our customers is paramount, demonstrating our commitment to their trust and satisfaction.”
Continuing the story, Tokyo Fabrics invited the BFG team to its factory in Wednesbury, near Birmingham, to experience the fire-retardant application process in person, as well as show off its rather impressive stock holding capability. It’s fair to say, the business is true to its word that they really have plenty of stock – in fact, Tokyo Fabrics currently holds over 30 million meters in stock.
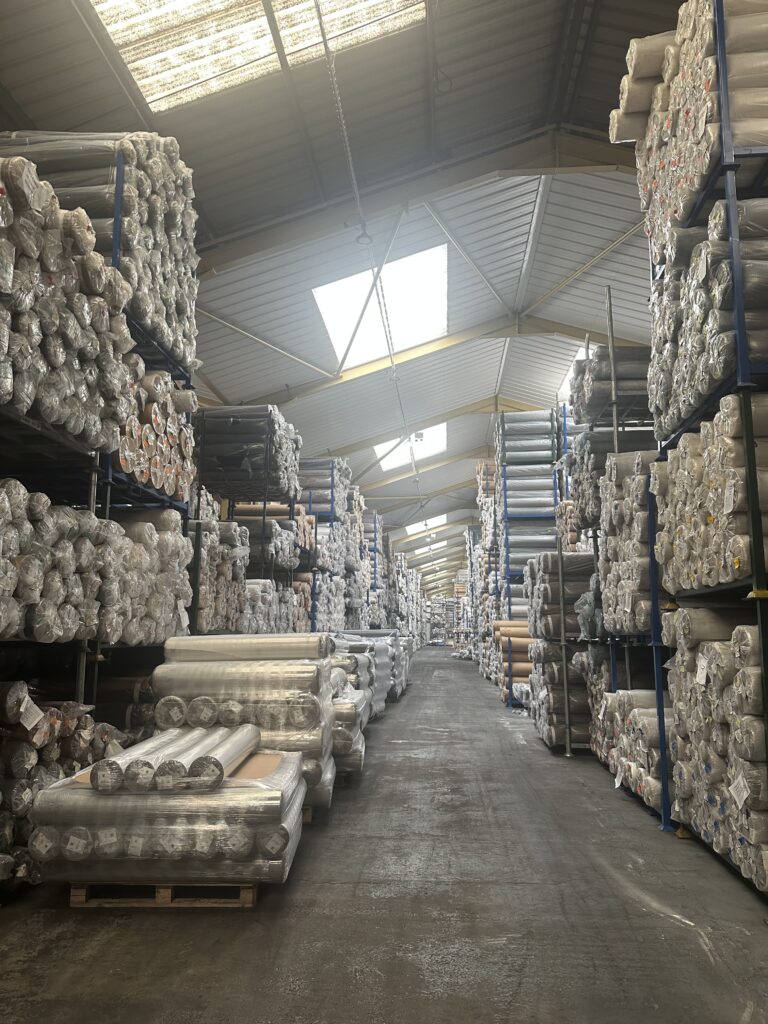
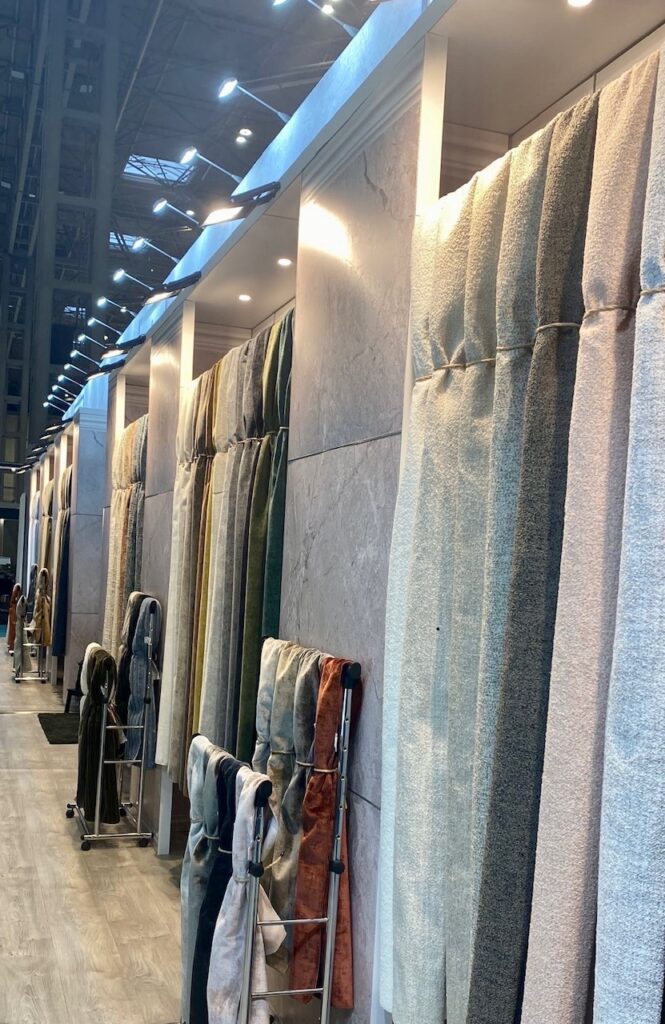
Upon arriving at the first facility – yes, there’s two, and plans imminently earmarked for a third site, Jag was quick to praise the entire team that makes Tokyo Fabrics tick, as he spoke passionately about the business, its journey and emerging from the noise and challenges it had to combat. Year’s later, the company has grown to be a staple in the fabrics industry and one that others in the space often refer to for FR treatments, fabric sourcing and general advice. In fact, over the last two decades, Jag has seen many of his visions for the business come to fruition, which is all down to hard work and believing in what the company provides.
For example, during the Covid pandemic, Tokyo Fabrics invested in new machinery and other elements of the business when others at the company politely questioned the strategy at a time of uncertainty across the industry. It was Jag’s sense and foresight that prevailed as the investment in expanding FR treatment production really paid off post-pandemic. Remaining humble, Jag said that he often goes with his “gut” on decisions and has always “invested back into the business” to continue its growth. However, when quizzed on future visions, Jag remained tight-lipped for now!
Walking through the factory, which had a new showroom smell about it with a capability of producing a million meters a week, showcased the FR production line in full swing and gave a real insight into the complexity of the process. While the machinery does the heavy lifting, the secret formula lies within the implementation and control. The natural flow from massive frames rolls the fabric through specific treatments for specific fabrics. Going through stages of application, heat, to then natural cooling, the end result is an extremely soft, finished touch to the fabric. It’s a process that you could actually stand and stare out for some time!
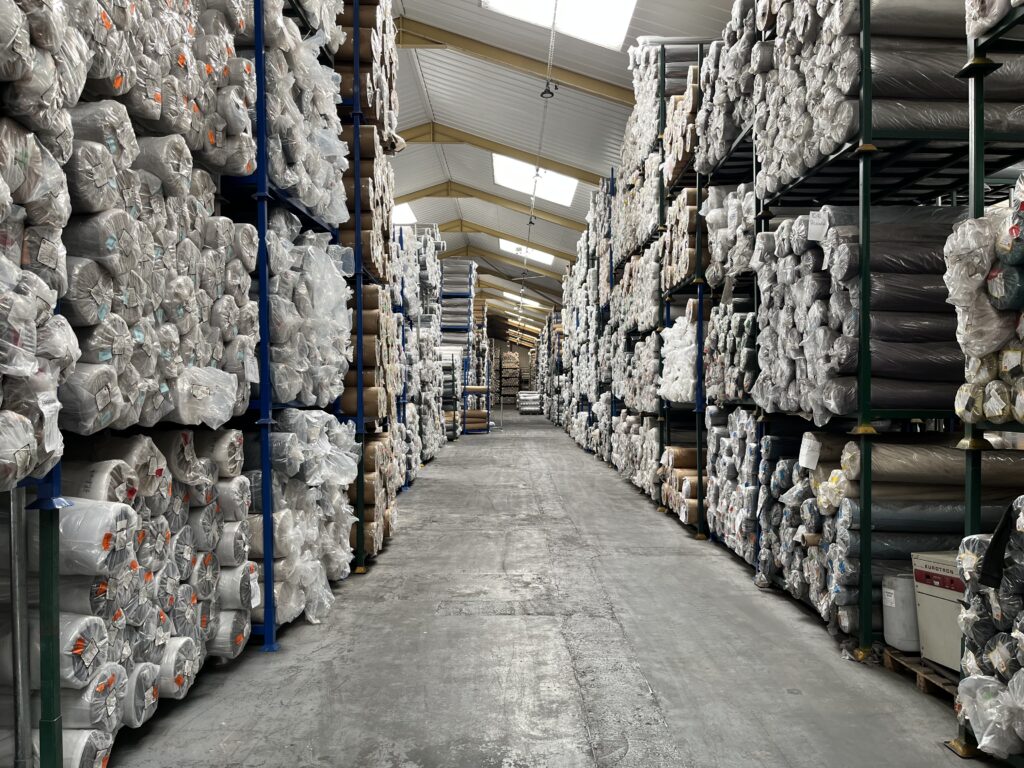
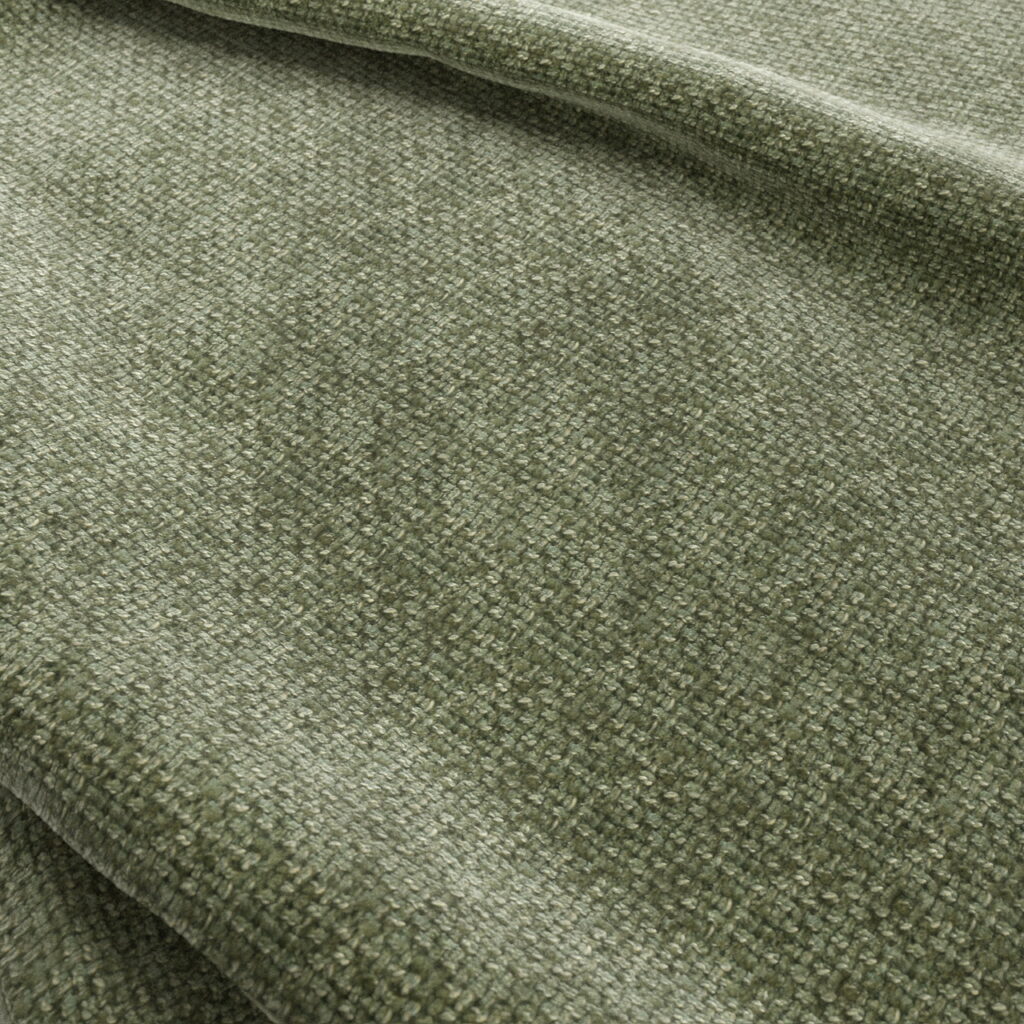
Another jaw-dropping sight was the amount of fabric rolls on display. It seemed like an endless maze from section to section as we moved from production to the testing area, where they test many fabrics daily.
“Unlike some FR specialists, we are proud to conduct fire tests for our customers on any part of a roll from any single roll at any time,” Jag said. “The journey then proceeds through a laboratory fire testing where our technicians rigorously apply fire to test its FR structure. Tactical burn test – besides the legally required x2 20 second tests, we also conduct a 25 second and 30 second test which is not required. Once confirmed, it is documented and only then is FR fabric released onto our shop floor – stored amongst the millions of meters we generate yearly.”
In fact, when customers visit the factory, Tokyo Fabrics encourages them to pick any roll at random for testing, which is then done live if requested to do so. From the test facility – and back through the maze of fabric rolls – we found ourselves at the compliance room, which is all about maintaining quality. Shading is one of the biggest factors to consider, alongside many other things with fabrics. Tokyo Fabrics employs a team to cross-check the products to maintain consistency and quality. It’s a daily operation and very thorough process, with master samples at both key sites of the company, including from China, for consistency purposes.
Wrapping up tour one of the first factory, just a short drive away is Tokyo Fabrics’ second facility, which has the most rolled fabric stored our editor has ever seen – and most likely the most across the UK and Europe! It really is a sight to behold. Just rows, columns, aisles full of fabric ready to go. Again, maze-like, we navigated our way to the largest FR treatment machine at the company alongside another FR line, which were acquired during Covid for a sum of several million. The beast of the two also has traces of bespoke design by Jag to enhance the cooling process for more delicate fabrics, with Jag describing the machine as the equivalent of having a “Rolls Royce and a Ferrari built together”.
The facility is also home to Tokyo Fabrics new showroom, kitchen space and offices, which at the time of the visit, was almost complete with finishing touches the only thing left to do – other than moving its HQ across. Furthermore, the company is continuing to invest at the site, with updated signage and other machinery, while plans are imminently afoot for phase three of its ongoing expansion.
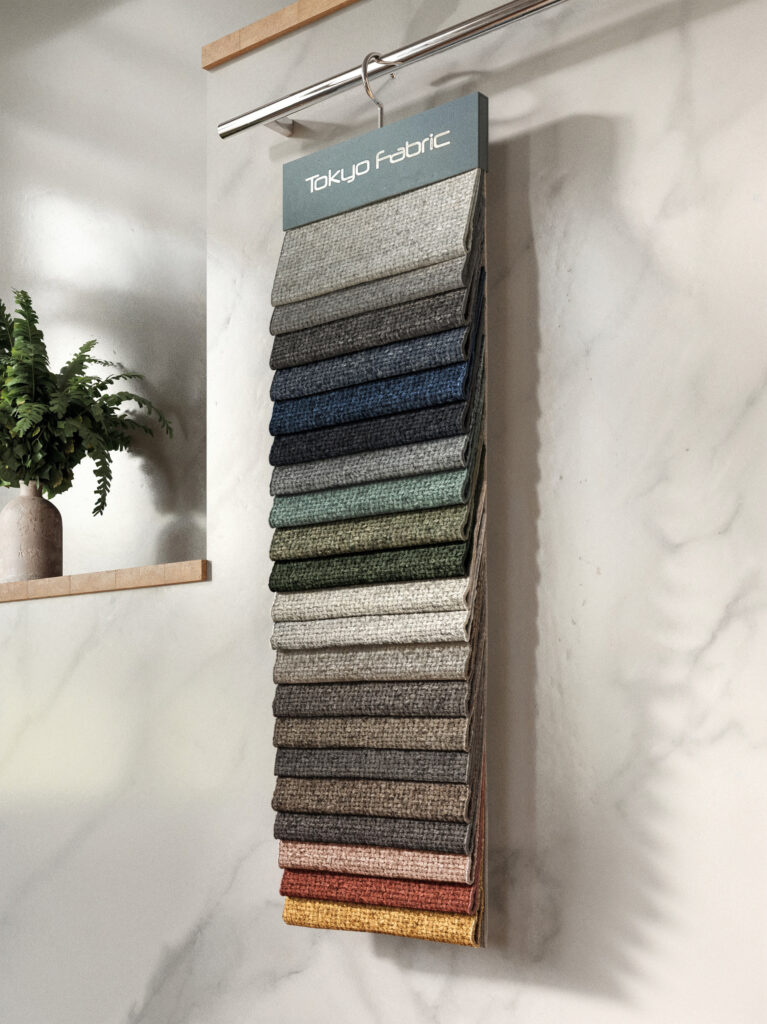
“Phase three includes our third factory site on 7 acres of land at the back of our second facility,” Jag revealed. “This expansion, which has seen our plans already approved, will expand our capacity by another 100,000sqft and will see in excess of £10 million invested into the project, which is all self-funded. All our investment is organic, and it’s something to be proud of as we have paid up front in full for all our assets.”
Another of Jag’s visions is to grow Tokyo Fabrics to be the “absolute brand in the space and to be as known as Nike but for fabrics”, with its latest investment plans pushing the company closer to his target. While plans are in place, Tokyo Fabrics – and its strong growing staff, will continue to work hard on doing what they do best.
“Building trust and our brand over time has been key to our growth as well as combating challenges along the way,” says Jag. “I’m confident in saying I don’t think there is anyone in our industry holding as much stock as we do”.
“Our growth is down to our amazing team and people behind the business like my father, Tarsem Singh Sandhu. We’re very lucky to have my father in the business, who is 80 years young. He’s been, and continues to be, a big inspiration for our family and entire organisation.”
As the tour came to close, it remains clear that Tokyo Fabrics is building something special. When phase three turns from Jag’s vision to reality, hopefully another invitation will be in the post. A final word must go to Team Tokyo, who provided an exceptional tour and made sure we didn’t get lost amongst the vast fabric rolls on display, and to Jag on his passion for all things fabrics and FR, who shared a final note: “We continue to engage and educate our customers about the differences in detail, which backed by intelligence and hard facts demonstrates our fierce pursuit of achieving absolute fire-retardant compliance.”