For British furniture manufacturer ercol, developing talent across all areas of the business is paramount to futureproofing its business. One channel that is vital to the company is through its apprenticeship programme, an initiative that has been running for almost 10 years now. We caught up with Roy Graves, Technical Support Manager at Ercol, who shares an insight into the success of its apprenticeship scheme, the importance of the programme and why the wider industry should adopt such an initiative.
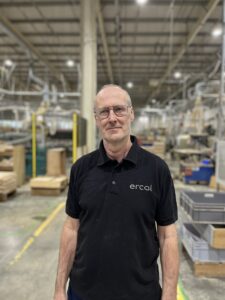
ercol and apprenticeships?
Apprenticeships have been a core offering at ercol for a number of years now. We re-established our apprenticeship scheme in 2017 to ensure we could have new people coming into the business to continue the legacy of the brand while managing an aging workforce.
We offer apprenticeships across a range of subjects, including electrical maintenance, machining, finishing/polishing, and assembly. This year, we are onboarding five apprentices who will be joining us at the beginning of August. We have two apprentices who are doing the computer numerical control (CNC) machining apprenticeship and two who will be doing a furniture manufacturing apprenticeship following the finishing pathway. Both of these apprenticeships are Level 2 courses lasting for two years each. We run these entirely in-house with our training provider, The Engineering Training Trust.
In our Assembly team, we have a furniture and manufacturing apprentice with Rycotewood Furniture Centre, our training provider for this apprenticeship.
Our apprentices gain valuable skills in safe and efficient working practices, and the variety of training they receive opens up multiple career pathways, ranging from design and development to manufacturing and installation.
Over the next four years, our plan is to take on a further three to five apprentices each year. We have also expanded the programme into other areas of the business such as maintenance and marketing. We currently have two maintenance apprentices and are planning the next intake for the coming months/year.
Our apprentices are important to us as a business; they bring with them fresh energy and new perspectives, often challenging us to think differently and explore alternative approaches to our usual methods. They also play a crucial role in helping us manage workloads, increasing our production capacity and enabling us to both ramp up the development of new products and bring back production previously handled by offshore partners.
One of the key strengths of our apprenticeship programme is its flexibility. This has allowed us to adapt in response to the evolving business needs. Despite these adaptations, we’ve maintained the core structure of the programme, as it continues to prove highly effective and rewarding for those who take part.
Success stories?
All of our Factory Section Leaders and Supervisors have been apprentices. Take our Facility Manager, Jordan; he came to ercol as an apprentice before taking over this position when the previous manager retired. Then there’s Tom, the Supervisor of the chair assembly area; like Jordan, he joined us as part of our first cohort of apprentices after we re-introduced ercol’s apprenticeship programme. Our older apprentices now fill vital roles in most areas of the business including Technical Design, Production Control, Purchasing, Upholstery Design, Prototyping, Stores management and Customer Service.
One particular success story that really stands out is our production manager, Brian Snelling. Brian had several part-time jobs before he undertook an apprenticeship at ercol. Despite having little experience in the industry, Brian completed a three-year apprenticeship in polishing and a two-year course in advanced polishing.
37 years later, Brian has inspired his family to undertake apprenticeships of their own. Not only has his wife completed an apprenticeship at ercol [in sewing], but two of his three children followed suit, completing apprenticeships of their own [outside the industry as an electrician and in childcare].
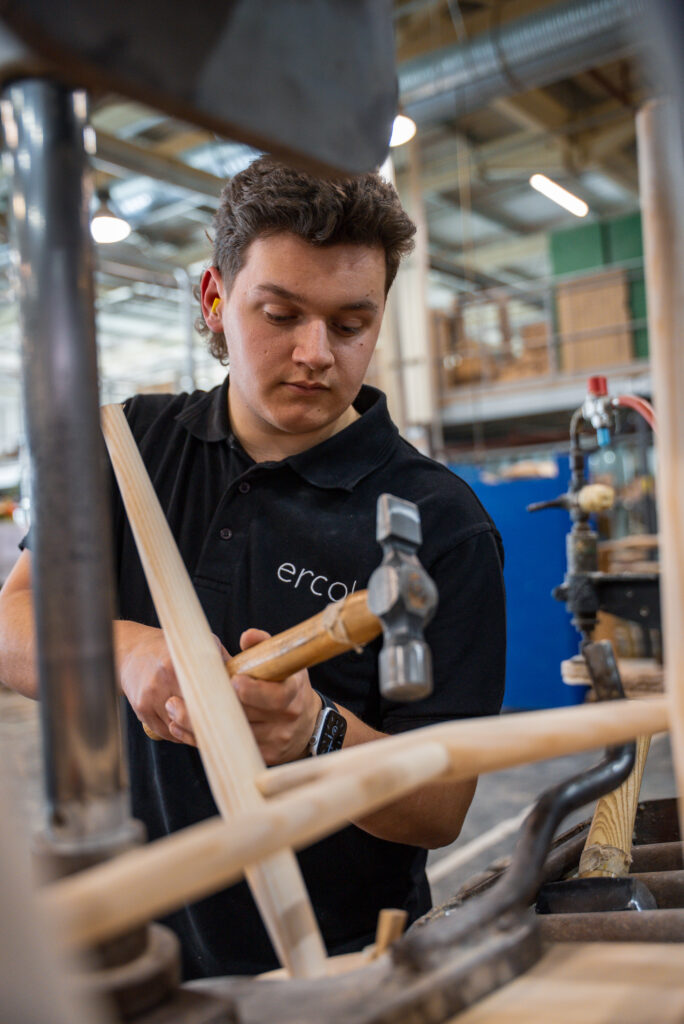
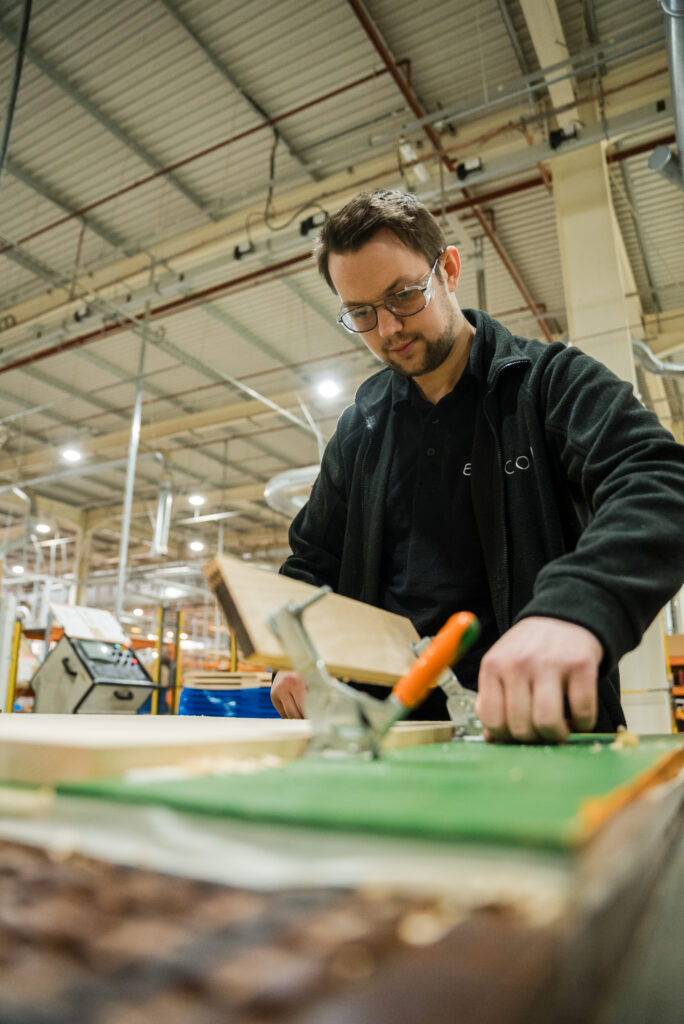
Investment into apprenticeships?
As levy payers, we use this to fund most of our apprenticeships, but this cost is just the beginning. We cover the cost of travel for our apprentices and provide a basic set of tools for them to use throughout their apprenticeship.
There are direct financial benefits for the business through incentive payments for young people, and reduced NI contributions for those up to the age of 25. However, the most valuable investment is time. We give our apprentices the time to develop and learn through their own actions, while also being there to support them throughout the apprenticeship.
The benefits the apprentices bring are more than just being another resource to allocate to a specific role. Their enthusiasm and different perspectives are channeled into improving our business practices.
Future plans?
We are reviewing the programme against our 5-year plan to ensure it is fully meeting the business’ needs in the current climate. We are happy at the moment with the subjects we offer to those in the factory, while always looking to see what is available for those in other areas of the business. We are also exploring what higher levels we can offer to those who have completed the apprenticeship to ensure they continue to grow.
Importance of apprenticeships?
Apprenticeships are hugely beneficial to the manufacturing industry. They help bring in fresh talent and plug vital skills gaps by training people in the exact skills your business needs, whether that’s working with machinery, learning safety protocols, or getting hands-on with the latest tech.
With an aging workforce and many experienced workers retiring, apprenticeships present an opportunity for these individuals to mentor the next generation of staff, ensuring their unique skills are passed on to help future-proof the business.
Overall, apprenticeships are a smart, practical way to build a strong, skilled team that will support you in this ever-changing industry. Our programme reflects the strong family values at the heart of ercol. We want to see today’s trainees grow into tomorrow’s mentors, passing on their knowledge and helping the next generation continue the cycle of learning and development.
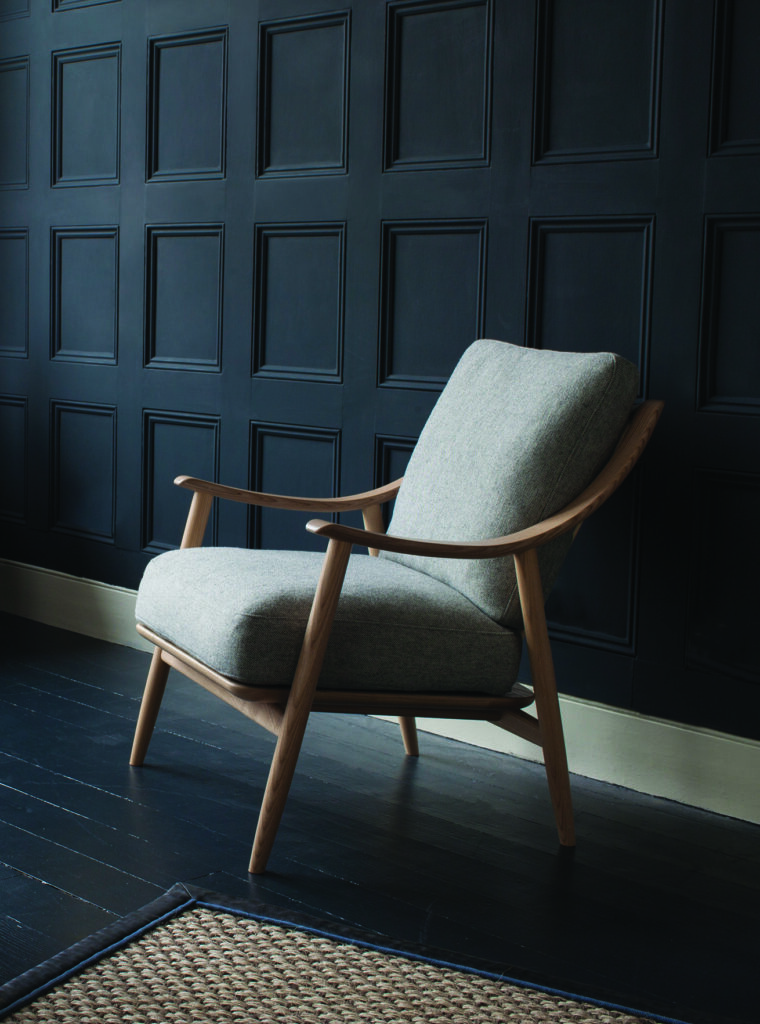
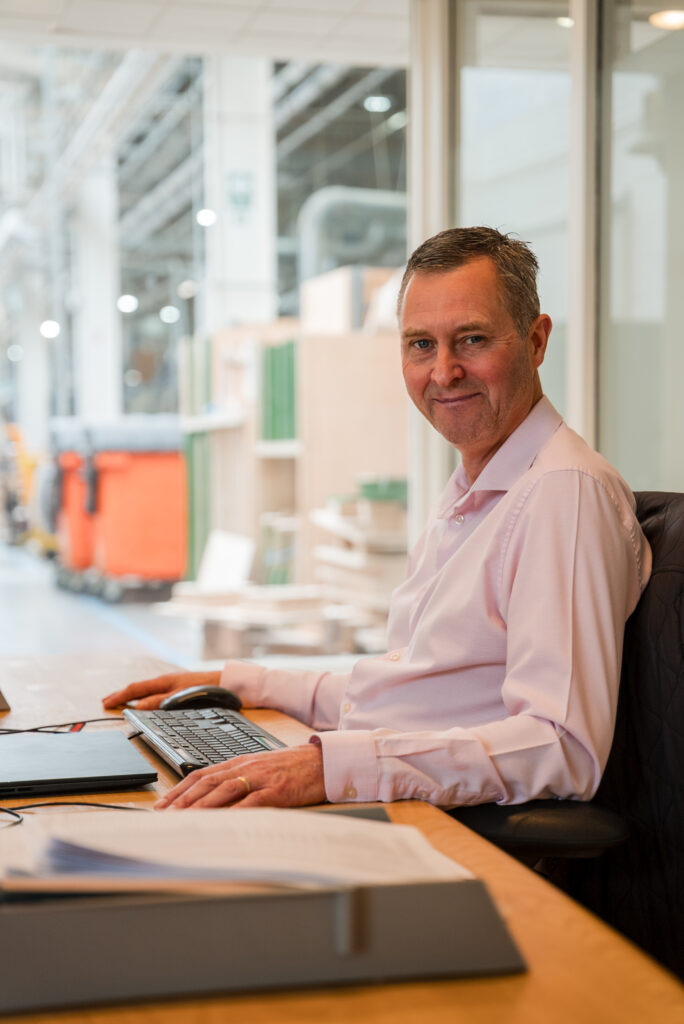
Apprenticeship pathway?
We work with other organisations to support and promote apprenticeships. Finding the right training provider is a big part of making it all run smoothly. They can help you with finding and recruiting the right candidates. They’ll also work with you to shape the apprenticeship around your business’ needs. Keep in mind, apprentices might also pick up skills that don’t directly apply to your work, but that’s actually a good thing because it makes them more well-rounded and adaptable.
If you’re not sure where to start when reviewing your training options, the Skills for Life website can also help; it maps out all of the training and employments schemes available, with support on how to implement these across your workforce.
It’s also worth getting involved in local careers events, especially ones run by councils or local schools. These are great opportunities to meet other businesses who are already bringing in apprentices and hear about what’s worked for them. Plus, schools are full of potential future talent, and building those relationships can benefit both sides. You’ll also get a better feel for which providers are out there, what courses they offer, and how others are making it work which is useful information when deciding what’s right for your business.
To find out more about how apprenticeships can benefit your business and to explore the training and employment schemes available to you, search Skills for Life website.