Working with clients across the domestic and contract upholstery sectors, the Peak Converters Team have been converting foam and fibre products from their factory in Derbyshire for the last 50 years.
Known for their outstanding customer service and innovative, high-quality products, they are the UK’s leading supplier of upholstery kits to the trade and produce around two million kit components every year. These are assembled and supplied as upholstery kits or cushions to some of the largest furniture, caravan, and mobile home manufacturers in the UK.
Whilst furniture is their bread and butter, the company also manufactures components for hundreds of other applications, from car sponges to pipeline pigs, converting a total of around one thousand tonnes of foam and 250 tonnes of fibre annually.
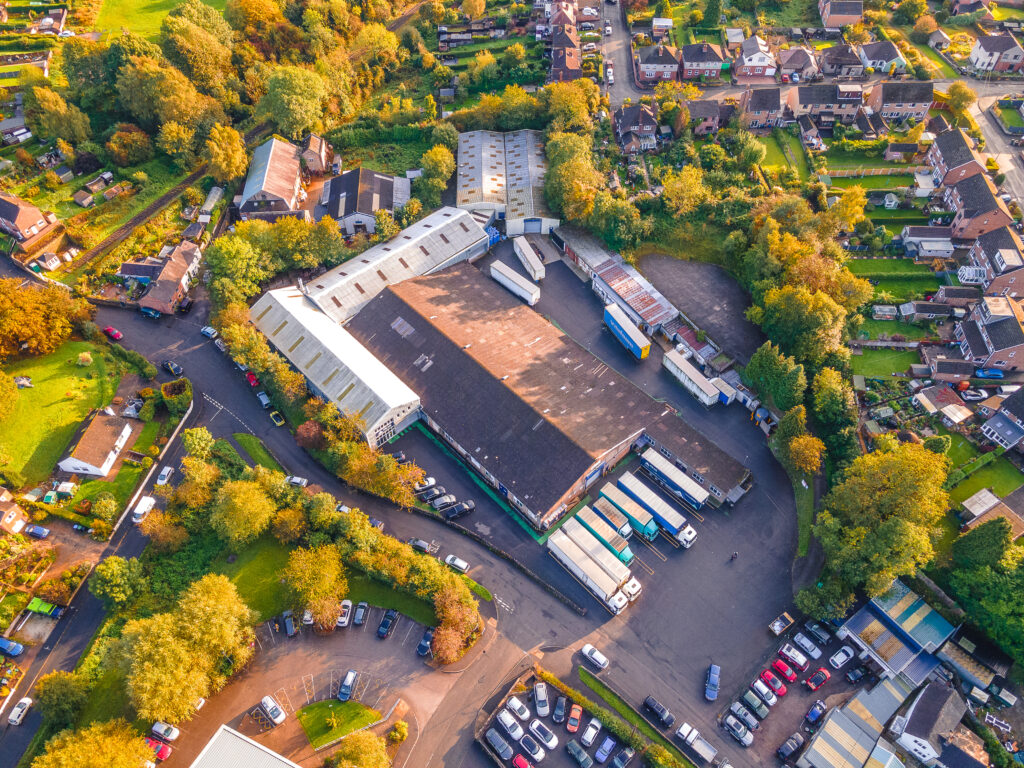
As part of their commitment to moving towards net zero and improving their environmental impact, the company, under the leadership of MD Mike Crowshaw, has introduced several continuous improvement initiatives throughout their design and manufacturing process to minimise foam and fibre waste during production, including a fully integrated, automated nesting system.
By its very nature, conversion is about minimising waste to get as much product as possible out of every block of foam or sheet of fibre. Peak are enormously proud to say that waste foam and fibre never ends up in landfill directly from their factory. In fact, there are several outlets through which waste product (trim) is managed, including sending it back to the foam manufacturers where it is repurposed into reconstituted foam. Reconstituted foam can be used in applications such as gym mats, underlay or upholstery. In addition, the company also creates its own crumb for use in applications such as cushions and soft play bags.
Good stock management is critical to minimising waste with every foam block or fibre sheet, as well as part blocks, being tracked so it can be used for sampling and small part runs. Peak’s reputation for handling trim well, and keeping it exceptionally clean, has seen the company become preferred supplier to several fibre manufacturers as it’s use has become more mainstream over the last few years.
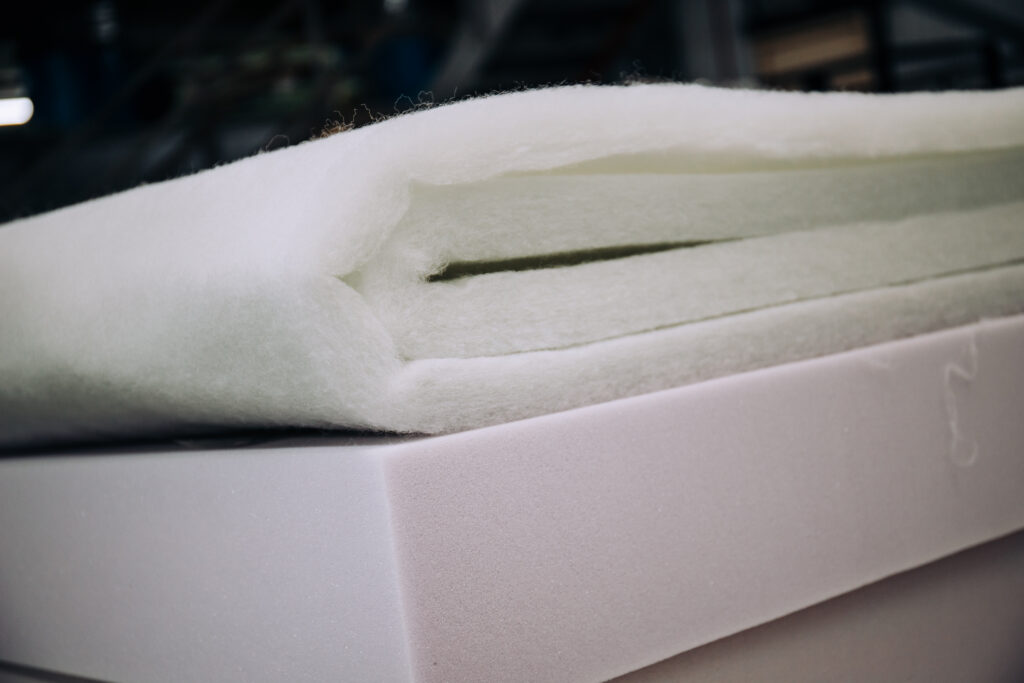
So where does the company see the future?
Says Mike “We have seen many manufacturers switch from foam to fibre over the last 5 years following chemical shortages in the foam industry and an increased demand for more environmentally friendly raw materials. I expect this shift will continue as fibre manufacturers improve their products and create materials which offer similar comfort and longevity to foam. Having said that, I don’t think foam will completely disappear. Foam manufacturers are working hard to remove chemicals and create more recyclable products and we are well placed to help them test the applications for those.”
To find out more about Peak Converters, please visit www.peakconverters.co.uk