Murray RoystonWard, Compliance & Sustainability Manager at Siren Furniture, talks about sofa recycling, legislation changes and what it means for the business and industry.
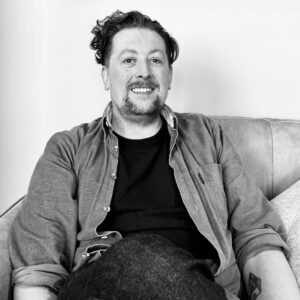
Siren Furniture, an FSC® Certified (FSC® C137929) designer and sourcing manufacturer of made-to-order upholstered furniture, is known for its commitment to product innovation, sustainable practices and high-quality production.
At the start of this year, Alan Spencer, Managing Director at Siren Furniture, shared his view on proposed regulations for fire safety standards, recognising the need for change to allow for innovation, sustainability, and circularity, within the supply chain.
As the year draws to a close, Siren’s Murray RoystonWard, Compliance & Sustainability Manager, turned the attention to recycling and how legislation changes in Scotland have come into play following its introduction across England. “Here at Siren, we have spent some time imagining what recycling a sofa might look like,” Murray says.
“In an ideal world, your sofa might last a lifetime. Fashion cycles dictate you are more likely to look to change your sofa before this though, and even high-quality fillings and cover materials will eventually show wear and tear. To help with this, we have been exploring furniture design with repair and reupholstery in mind. For example, construction and upholstery methods that make it easier to strip off materials and replace them; or cushion designs where individual components can be easily swapped out for new.”
However, “repair won’t always be the answer”, Murray continues, and, at some point, an item of furniture will come to the end of its life. “In an ideal world, these easily strippable designs would be broken down for parts that can be reused. Already, we see foams made from recycled foams.
“Perhaps, one-day, this will easily be extended to fibres, timber, and beyond. This is a vision of circular economy where end-of-life materials become inputs for new materials. Whilst there are still some technical barriers to some of the above, broadly speaking, this is quite achievable apart from one major hurdle. That of chemicals used for Fire Safety.”
In 2023, new rules were introduced regarding the disposal of upholstered furniture. Similar legislation has now come into effect in Scotland. The main purpose of these changes is owing to the presence of Persistent Organic Pollutants (POPs) which do not break down in the environment. Murray added: “POPs cover a range of chemicals which accumulate in the environment and are harmful to health. Historically, POPs have been used for Chemical Flame Retardants (CFRs) within, for example, foams and fabrics. CFRs, of some form or another, are, unfortunately, completely necessary in order to comply with the UK Furniture Flammability Regulations (UKFFRs).
“The UKFFRs are generally considered outdated and are currently under review, something we have been generally supportive of as we hope it will allow for the necessary innovation to maintain fire safety in ways that improve the health and wellbeing of consumers and the environment. CFRs are, themselves, a complex subject.
“Historically, brominated flame retardants, including deccaBDE, have been of especially high concern. They have since been heavily restricted and voluntarily removed in the UK. Other CFRs remain in use. CFRs are, however, perfectly legal. REACH legislation regulates chemicals, and upholstery must conform to the limits given.
“So, in order to sum up this complex picture, upholstery requires the use of CFRs in order to meet UKFFRs. CFRs, in their current form, are both legal and, based upon current legislation, considered safe. Historically, less safe CFRs have been used, leading to concerns about their disposal in landfill.”
This picture, however, gets more complex, as Murray explains. “What is considered a legal limit can change as new knowledge is gained. Restricting the use of one chemical formulation can lead to the use of others. Sometimes these replacements lead to new, unexpected problems; what is known as a ‘regrettable substitution’.
“As a furniture manufacturer, whilst we are confident that our products are both legal and safe, the chemical details of the CFRs used by material suppliers are often unclear. What Siren would, therefore, like to see is better chemical transparency. Ideally, fire safety would be achieved without chemicals but, where they are necessary, consumers should be aware of all the details. The hope is that such transparency would help drive further reductions in the use of chemicals.
“So far, we have focussed upon chemicals and their risks to health and environment but, returning to the question of recycling. At present, it is very difficult to recycle a sofa. For example, CFRs mean that materials such as foams can’t be readily collected, broken down, and recycled into new foams. Where recycled foams are available, manufacturers have sourced used, end-of-life foams from outside of the UK to ensure that they do not contain CFRs. CFRs and, by extension, the UKFFRs, are currently a barrier to circular economies and improving the sustainability of upholstery.”
The most recent UN ‘Emissions Gap’ report paints a glum picture of failing to meet necessary actions to restrict global warming to 1.5°C. “Chemical transparency and fire safety without CFRs are both essential components of creating more circular and sustainable products in support of global emissions targets,” Murray says.
“Siren’s focus, therefore, is in advocating for changes to UKFFRs and increased chemical transparency. We are keen to develop ‘circular’ products and are actively looking at how we can design products to better support this but, ultimately the present status of CFRs will always be a barrier to change.”