We share inside access following our recent trip to Swedish bed and furniture manufacturer DUXIANA.
Back in April this year you may’ve come across one of our articles on the partnership between Tottenham Hotspur Football Club and Swedish bed and furniture manufacturer DUXIANA. A few months on, Big Furniture Group was offered the opportunity to either lace up our football boots and don it with the likes of Kane and co, or be put through our paces across three factory visits to find out just why the DUX Bed has gained global success. Naturally, and the obvious choice, was to try our hand at making some beds. Plus, having already been to Spurs and on the receiving end of a 5-0 thumping last year – we were keen to explore new settings.
Arriving in Sweden, the first stop of the three factory tour was located in Sösdala, just a short drive, which at times looked very similar to our editor’s Norfolk roots, from Malmö. Greeted by a nostalgic spring making machine – and current CEO of the four-generation family business, Henrik Ljung, it immediately gave the impression of what was going to be displayed. Lots of history. “The family are hoarders,” Kevin Slade, Head of Next Gen at DUXIANA, said with a smile. “Obviously in a positive way!” And there’s good reason for it. DUXIANA has built its reputation over the last 90+ years due to the success and innovation of its core component, the DUX spring. The manufacturing process remains top secret to outsiders, and while no photos were allowed during the second factory tour – more on this later – there is truly a remarkable operation in place.
With regards to ‘hoarding’, the brand keeps hold of every machine and even design template to make sure none of their history is lost. It goes without saying, the storage facility requirements are on an impressive scale – so much so, the business has recently invested in more space just down the road, which is to house an expanded showroom and museum. Back to the current building, factory one, as we’ll label it for the purpose of the article, solely focuses on furniture production, including DUXIANA’s most famous model, the Jetson chair. Around 20 staff, all equally trained at each station, which takes between 12-18 months to master from rubber wrapping, tufting, gluing and adding the finishing touches, operate the factory, which is stress-free, calm and calculated.
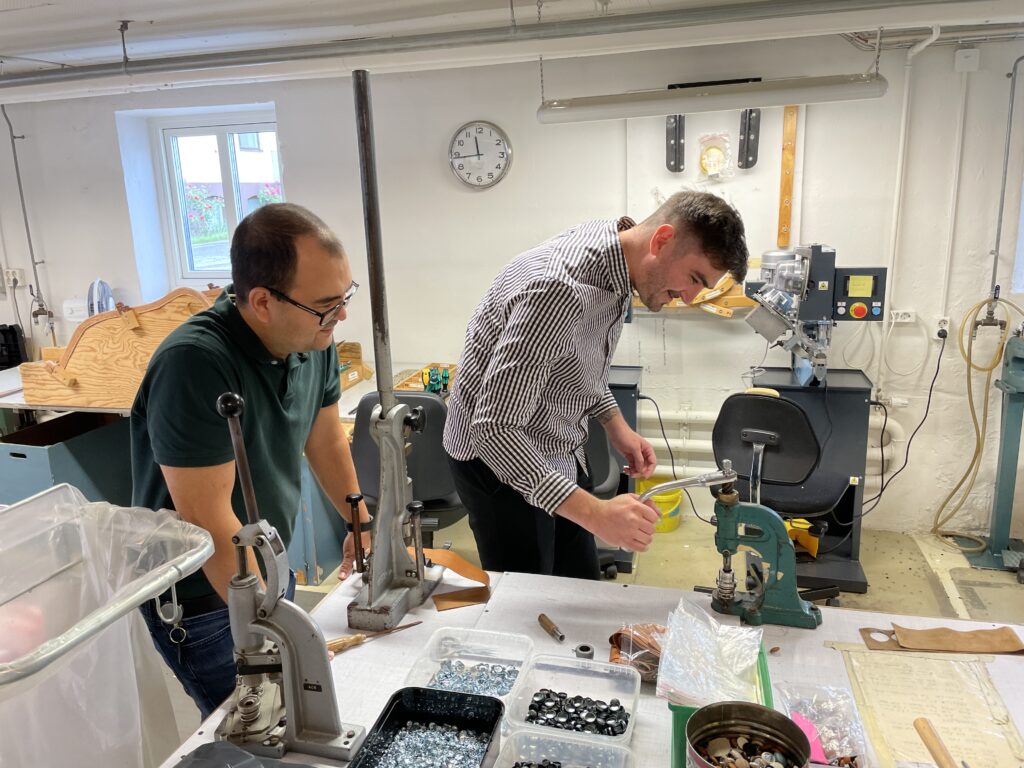
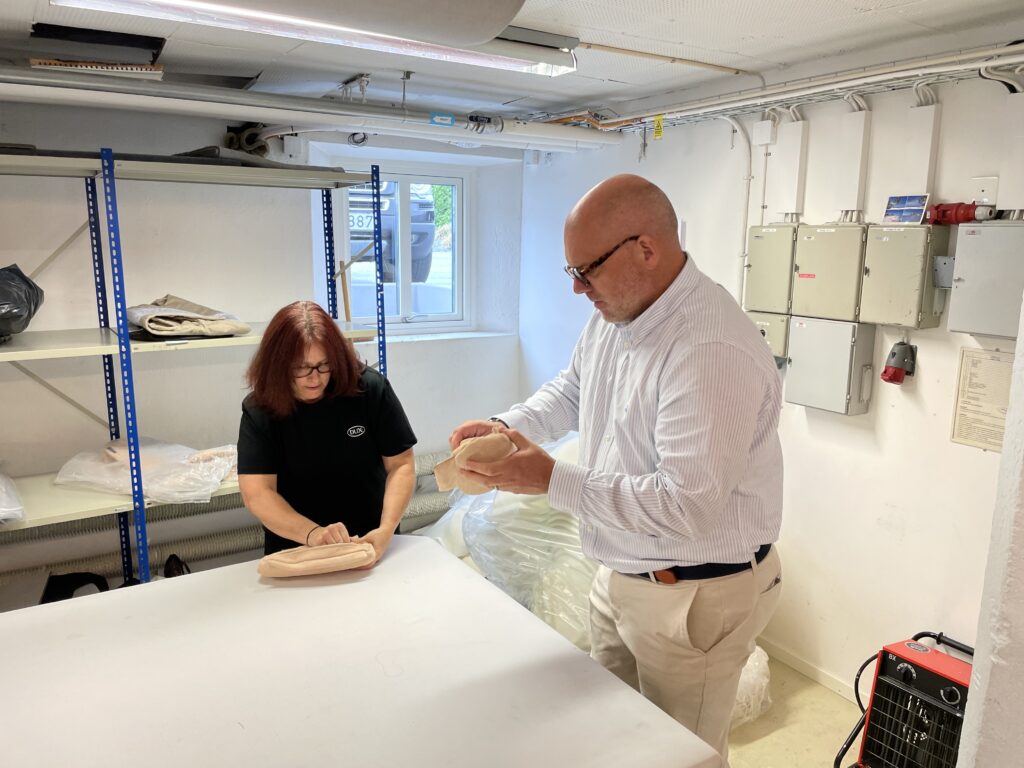
“Plenty of the team here have been with us for decades,” Henrik said. “One employee has been with the business since 1980 and we have generations of families that work with the business, all mainly based in Sösdala too. A recent worker, who has now retired after 42 years, actually moved away in the last 10 years before retiring but didn’t want to leave and commuted by train two hours each way to remain here. We look after our staff and it shows in the products we produce too.”
Attention to detail is key. Every employee was happy in their work too, which is all part of the wellbeing and family essence the business implements. Moving through the stations, we got the chance to hand press a button, while also learning that every single button made is hand pressed. That’s a lot of buttons. Although eager and full of enthusiasm, its best to leave the craft to the professionals. In keeping with the detail, it was here that we also gained an insight into all the components that make a DUX Bed – a bed that breathes, as well as being able to see inside before we set off to factory two.
“The DUX Bed is comprised of customisable components. Each component is replaceable and some even upgradable,” Henrik said. “Our top pad is not fastened to the bed for greater flexibility. The top of the mattress unzips to allow access to the Pascal customisable support system and the dual spring bases operate independently of each other. The result is a bed that cannot only be restored as it shows wear, but may be improved with the release of new accessories and technological innovations.
“An important and overlooked benefit of a spring system derives from the fact that the bed is essentially hollow. This allows air flow to be generated by the user’s movements. The streaming air can not only shuttle body heat out of the mattress, but can also produce the level of ventilation necessary to help combat odours, bacteria and fungus.”
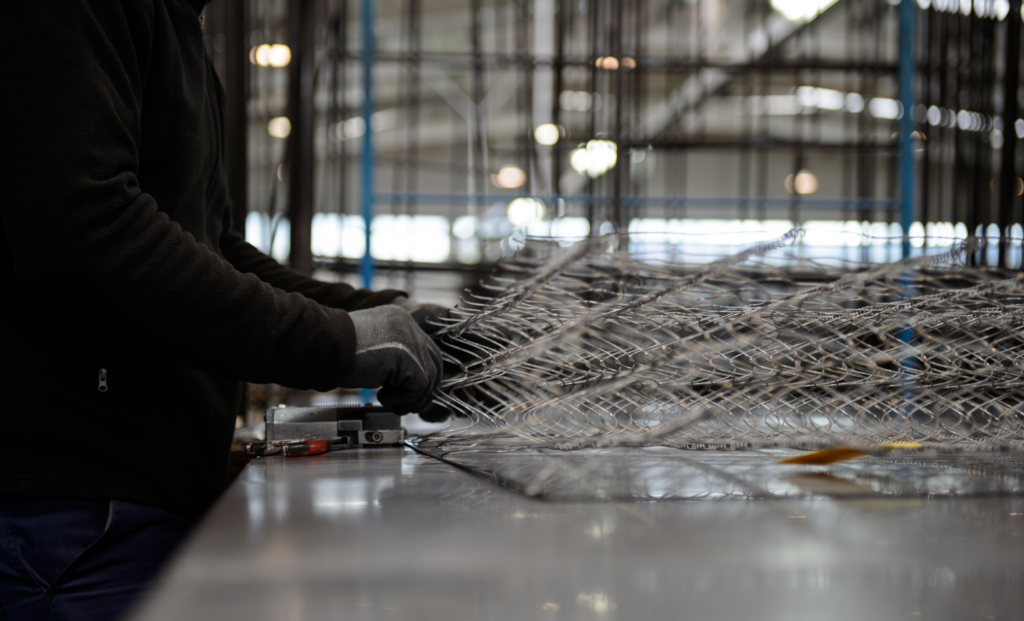
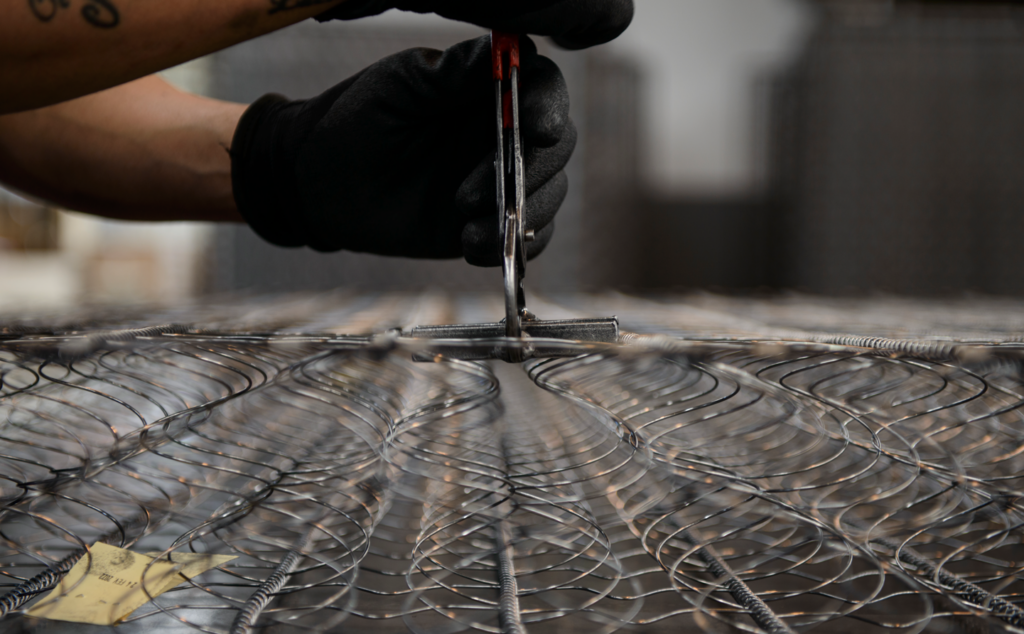
In fact, the DUX Bed spring system, including its Pascal springs enhancement, is guaranteed against breakage for 20 years, but very often last beyond 30 years. As well as longevity being at the forefront of design, as is sustainability. “The idea behind the renewable design is that the DUX Bed may be the last bed you’ll ever need. Highest-quality materials coupled with over 90 years of heritage of Swedish craftsmanship result in a bed made to last. Simply put, the longer it lasts, the fewer beds will end up in landfills,” Henrik added.
DUXIANA is also a recipient of the Oeko-Tex 100 Certificate. The Oeko-Tex Standard 100 is an independent testing and certification system for textile raw materials, intermediate and end products at all production stages. This certificate confirms that their beds meet strict human-ecological requirements, being completely free of unhealthy or harmful chemicals.
Furthermore, the bed base is constructed with wood harvested from Northern Sweden, where bitter cold winters produce a slow growth pine that is “unmatched in strength”, while strong Swedish steel is the backbone of every DUX bed. The unique continuous-coil design, coupled with the finest steel allows DUXIANA to make one of the smallest, thinnest and most dynamic springs on the market. The latex used in DUX beds is a natural product harvested from the hevea or “rubber” tree. The latex in its top pads improves longevity and provides contouring support.
With support in mind, The DUX has been designed to keep your spine in line, as Henrik explains: “When you sleep at night, your back does not necessarily get the rest it needs. Not having the right support can cause tension. That is why we design our products to align your spine through dynamic support. Imagine sleeping on a bed that adjusts to your shape and body movements. How does it influence you? Natural position, relaxed muscles, less pain, better blood flow, and a chance to fully restore your body overnight. The DUX Bed gives you all of that.”
Digesting the full brief ahead of seeing the bed production in the flesh, attention turned to a number of industry first’s that DUXIANA has claim to, although the business remained modest when highlighting. Kevin said: “DUXIANA have long been innovators and market leaders in a number of areas. We were the first at creating a framed bed, the top pad, our Pascal customisable support system, a mono brand bed store, the cut through retail display and that we own a hotel with our beds in. We don’t always like to shout about it but our history is rich and we’re proud to be pioneers in our field.”
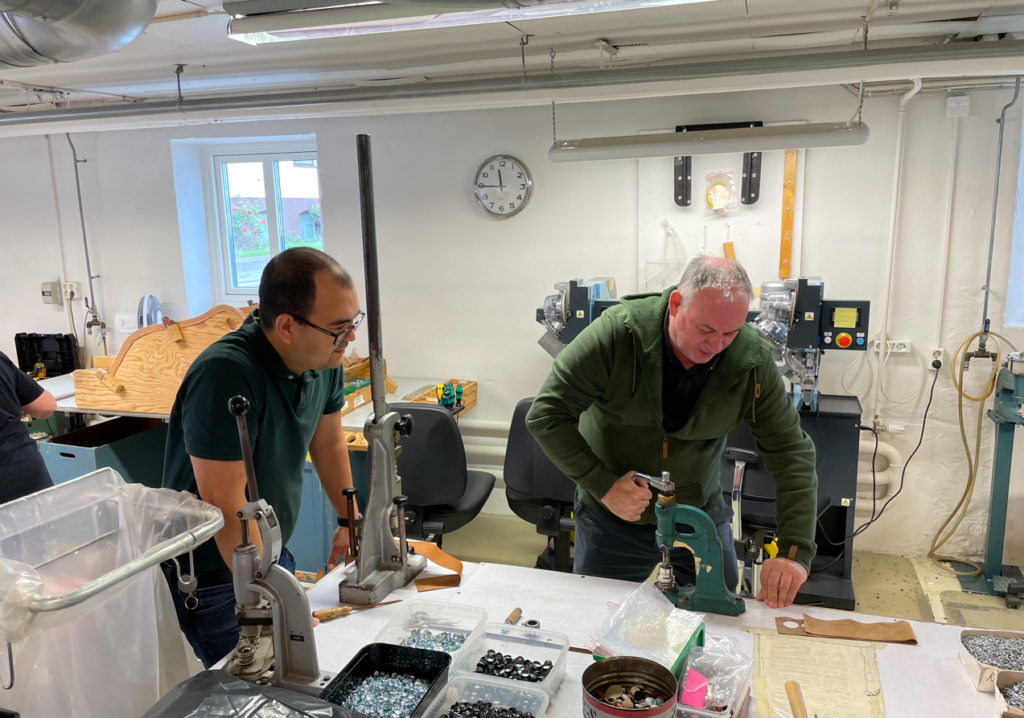

As mentioned earlier, DUXIANA is in its fourth generation of the Ljung family, which also currently includes Anders, Oscar and Charlotte, who alongside Henrik, are the great-grandchildren of founder Efraim Ljung. The business to this day remains 100% family owned and operates in more than 30 countries and over 300 stores. However, the family business of bed making could’ve been a completely different industry. Henrik told the tale: “Back in 1924, Efraim, who was then a chocolatier, checked into a small hotel in Chicago, USA, and was fascinated by how comfortable the bed was. Using a small pocketknife, he carefully cut open the mattress to discover flexible springs inside.
“After sketching out drawings and repairing the mattress, Efraim shifted his focus from his confectionary business and began devoting all his time to experimenting with flexible steel springs of varying strengths and elasticity. He formed DUX and began manufacturing mattresses in Malmö in 1926.”
Refueled and ready to take on factory two, which is based in Santo Tirso, just outside Porto, Portugal, this facility is where the magic happens, with production of the springs and beds all under one roof. Taking us through this leg of the tour is Henrik’s younger sibling, Oscar Ljung who was full of energy and passion, while keen for us to get behind the production line too. He even kitted us out in DUX shirts to make us feel part of the team.
“We make around 10-14,000 sleeping products per year from this facility alone. Everything is like clockwork and we’re consistently investing in our equipment to further enhance our processes,” Oscar said. “Our spring manufacturing line regularly gets tweaked and maintained to keep production efficient. The whole process is like a symphony of springs being put together.” He’s not wrong. Watching the springs dance their way through each stage from a steel line to becoming a coiled spring, to when they meet and ‘hold hands’ is a fascinating watch. Taking a closer look at the mechanics reminded us of an old 35mm film cinema projector going through the twists and turns before emerging out the other side as the main feature.
The DUX spring line machines are also made by the business to maintain their top-secret method of its springs, as well as full control. Following the initial stage of production, the springs move to another phase where we got the opportunity to get our hands involved once again. What can only be described as adding a layer of chain mail throughout the base, this part reinforces the structure. Feeding the ‘chain mail’ into the base is a crucial part of the journey, with plenty of spot checks made by the operator. Knowing what to look for is critical, so after a couple of ‘attempts’ we were glad to take a back seat with this part.
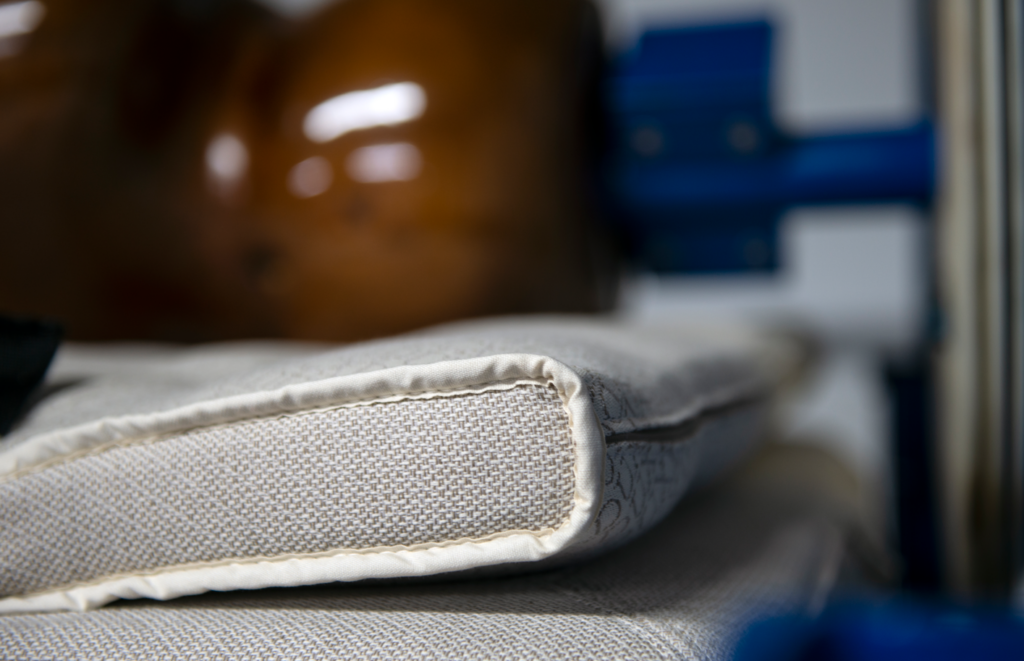
However, further down the line, the opportunity to staple the now-made spring frame to another framed structure was right down our editor’s street. In fact, Oscar had to intervene as there was plenty more to see. Guiding us through the numerous sections of the facility, we found ourselves at the testing bay, where we met chief product tester Fingal – a 110kg wooden dummy, shaped like a person – a far cry from the typical ‘roller block’.
“Fingal’s older than me!”, Oscar said. “Fingal has 70 years in the rolling business and acts like the actually shape of a person rather than an oval roller typically found in most testing. It rolls 24 hours a day – 600k times – representing around 30 years of use – in its typical cycle. We love Fingal!”
From heritage operations to recent investments took us to DUXIANA’s pocket spring machine, which was installed around one year ago and plays a key role in their frameless mattress-only models, where the base is pocket-sprung. “18 months ago, we launched a mattress range (for customers who did not need the complete bed set up) comprising of two layers of springs – one being the DUX continuous coil springs at the top so that it’s next to the body, the other being DUX pocket springs at the base away from the body but as a foundation, but they are not a regular pocket spring as we make them with our high quality wire coupled with the finest material for the outer case” Oscar added. “This newer machine has been an important investment for us and is part of our mindset to keep progressing as we discover ways to improve the products.”
Next up, and just a short trip from Santo Tirso is factory three in Vila das Aves, where they specialise in textiles for the beds, headboards and all of the furniture. Here, the seamstress division is in rows of experience – the further up you are, the more experience you hold, the top being masters of the craft. “The further in the factory, the longer they have worked there and they are deemed as a master of sewing,” Oscar said. “They all use the naked eye on measurements and quality – making it a learnt skill with experience. Again, families continue to work here through the generations.”
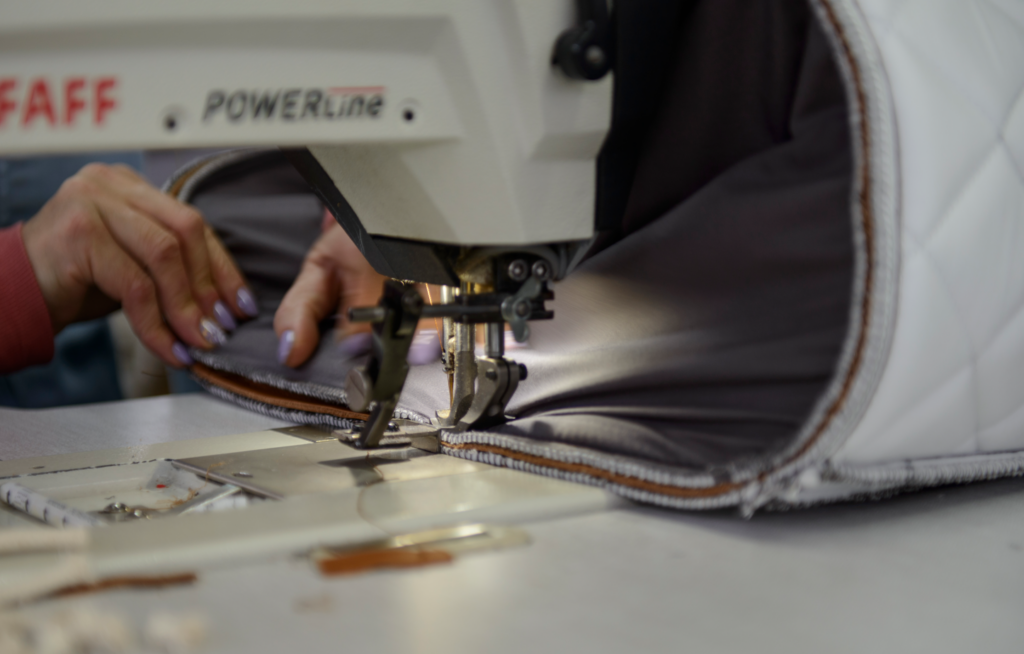
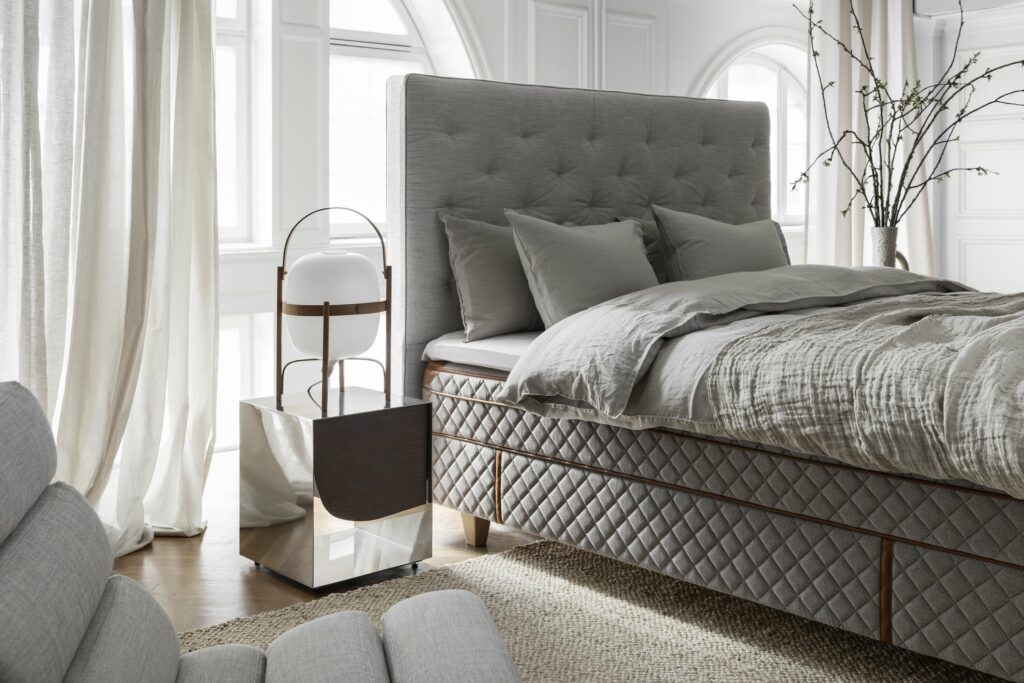
Oscar highlighted that double stitching is also key to their quality, while adding that even the DUX brand stamp that goes on the bed products all go through quality control. It’s also worth noting that product quality control issues are extremely low to rare at all three factories due to the stringent processes in place and the skills each worker employs.
The final thing left to do was to try out a finished DUX Bed. It’s fair to say we didn’t want to budge. While taking in the experience of how the DUX Bed is made, Kevin hinted at some future plans in the pipeline. “We are currently working on something new, which will be unveiled in Q1 next year, but that’s all I can reveal at this stage. We’re also well into the planning of our centenary year when the business will celebrate 100 years in March 2026. So, watch this space!”
Having had a glimpse at the current project in motion, it’s certainly one to watch. There will be more on this over the coming months, as well as a deeper dive into the products and areas already highlighted. We think we made the right decision in leaving the football boots firmly in the boot bag.